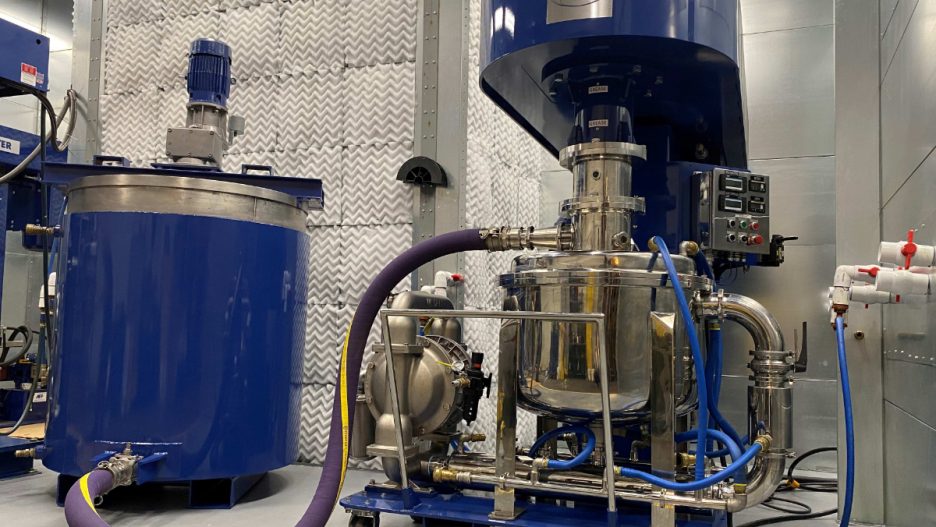
Case Studies
Case Studies: Successful Applications of Hockmeyer Equipment
Here at Hockmeyer, we are about far more than simply selling machines. Our state-of-the-art machines are unrivaled in our industry, and we strive to ensure that the same is true of our customer service. That is why our clients across a wide range of sectors come back to us again and again to help them solve all their milling, mixing, and dispersion problems.
In this post, we wanted to share three real-life examples of how we have supported our clients and tell you a little more about some of the additional services we offer.
The Case Studies
CASE 1: Carbon Black Pigment Dispersion
Our client’s carbon black pigment dispersion process was taking around six hours using a horizontal mill, a delay that was significantly cutting into their efficiency and profits. The client was looking to reduce this processing time, ultimately allowing them to turn over more batches per day.
Thanks to Hockmeyer’s NexGen Vacuum Recirculation Mill, we reduced this processing time to around one hour and 45 minutes. Our machine also offered a superior particle size standard and surpassed color development expectations. Overall, the client enjoyed a 70% reduction in milling time and tripled their milling capacity.
CASE 2: Ethylene Glycol Dispersion
Our client was struggling with lengthy milling times of around five hours, as well as foaming issues when dispersing in ethylene glycol. This client needed to reduce their processing time and eliminate the foaming, which was more than doubling the batch size during processing.
Our NexGen Vacuum Recirculation Mill reduced the processing time to just one and a half hours and minimized the foaming. The vacuum feature removed the air bubbles during milling, promoting more particle-to-particle collisions without the “cushioning” effect of the bubbles.
CASE 3: Agrochemical Concentrate Slurry
Our client’s previous solution produced an uneven particle size distribution and required a total processing time of around 72 hours in cascading milling progression through three horizontal mills. This client needed to simplify their milling process and reduce their total process time. They were also seeking an alternative solution that would be easier to clean between products.
They were able to reach the desired particle size with a tight particle size distribution after just two hours of processing in the Hockmeyer NexGen Vacuum Recirculation Mill, including 30 minutes of dispersion in a High-Speed Disperser with an “F” blade. The eventual result was a huge 95% reduction in total milling time.
Other Ways Hockmeyer Supports Clients
We offer a wide range of support services to ensure our clients can get the most out of their Hockmeyer machines and solve any problems quickly and easily.
Customer Testing
Choosing the best equipment for your processes is not always straightforward. In our testing lab, prospective customers can test out laboratory models of most of our popular machines to ensure that they are choosing the right tool for their needs. This initial testing is always free.
Parts & Service
When equipment goes down, it costs valuable time and money and has a knock-on impact on your clients. We keep a wide variety of replacement parts in stock for immediate overnight shipping. In addition, our experienced customer service technicians are on hand to advise you and keep your equipment running at maximum efficiency.
Field Training & Support
With dedicated training and support, we are here to help you maximize the potential of your Hockmeyer machine. We offer a range of services, including operator training, equipment inspections, process optimization evaluations, and virtual sessions for when you need help fast. Our support plans are available in six- or 12-month blocks.
Equipment Support Program
Your Hockmeyer machine is a significant investment that requires ongoing care and maintenance. With our equipment support program, you can identify and address small problems before they become bigger problems. Our support program includes a six-to-12-month post-installation assessment, equipment inspection, evaluation of wear-and-tear patterns, operator refresher training, and more.
Learn More
If you would like to learn more about any of our machines or service offerings or have any questions about anything we have covered in this post, please contact us today and a member of our team will be happy to advise you.