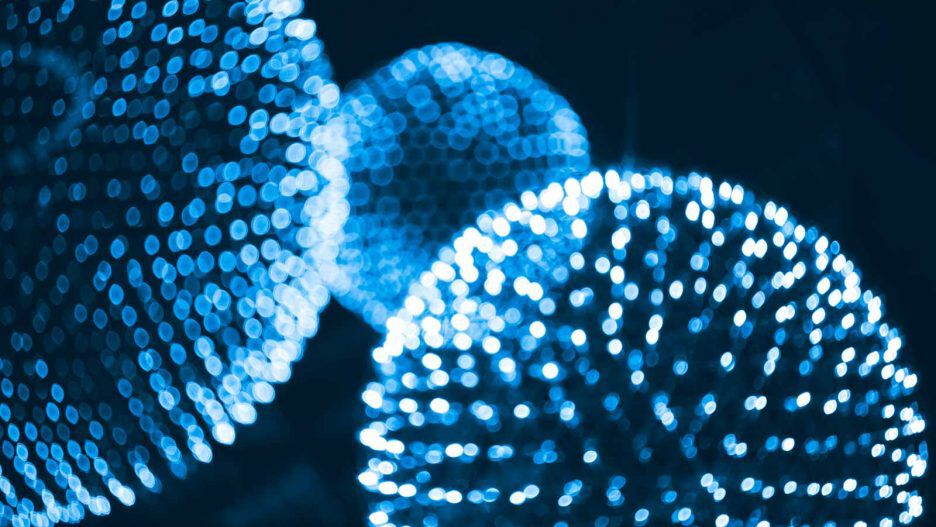
Publications
Faster Nano Dispersions
The HCPN is a specially designed mill for grinding particles into the nanoparticle range with very short process times. The new design incorporates many different changes in the internal milling system while leaving the fundamental, easy to clean and use aspect of the immersion mill the same.
OVERCOMING THE OBSTACLES
First was being able to consistently manufacture a media/feedstock separation device with highly accurate flow through zones that prevent escape of the very small media (.3mm and below) from the mill while simultaneously permitting high volume passage of the feedstock. Additionally, the total open area must accommodate the rapid throughput from a hyperactive media field without clogging.
Second was keeping the media in the grind chamber from escaping through the intake draft tube. Floatation as well as pressure increases in the screen area can cause the media field to expand into the void volume area within the chamber and cause the media to escape through the upper intake draft tube.
Third was preventing media from leaking through the machined tolerances between the bushing supporting the shaft and the shaft itself as it passes through the bottom screen of the mill chamber and connects to the suction propeller below it.
Fourth was substantially increasing the activity in the media field to allow rapid feedstock pass through while simultaneously accelerating the number of contacts per unit of time.
ADDRESSING THE CHALLENGES
THE SEPARATION DEVICE:
The first was overcome by the development of the *HOCKMEYER CONTAINMENT WALL* (multiple patents pending) consistent in open area size and with 43% porosity for feedstock flow. A technically improved and precise manufacturing process at Hockmeyer eliminated the use of typical screening devices using wedge wire or laser drilled openings which may only provide an open area of 10% or less.
THE INTAKE UPPER DRAFT TUBE:
Adding an auger to the upper draft tube of the mill chamber solved the second challenge. The auger plays several roles. The auger provides a consistent feed of material into the mill chamber during the start-up process and prevents the media field from floating during the initial immersion of the mill head into the batch.
The auger forces large agglomerates to stay in the milling chamber along with the media until they are small enough to pass through the screen. In this instance, the auger acts as a governor by allowing material in the upper draft tube to slip along the auger and not over pressurize the mill chamber. As a result of this governor affect, the media field does not expand and media loss through the upper draft tube is eliminated. Depending upon its’ rheology, the feedstock float may also be controlled through the size of the draft tube itself. The flow rate of over-sized agglomerates is controlled by the pumping rate of the auger. The disintegration of the agglomerates is controlled by the intensity of the bead field and the dwell time within the basket. Pumping rates can go up or down at any given speed by selection of the appropriately pitched auger. This allows for very high energy, hyperactive flow fields using very small media. Small media is considered to be at or below .3mm diameter.
THE SUPPORT BUSHING:
The third obstacle was eliminated by the development of the HCPN centrifugal peg hub. The hub was designed to generate sufficient centrifugal force to keep the media field away from the support bushing in the bottom of the screen.
INCREASING MEDIA OSCILLATION FREQUENCY:
As the size of media is reduced the number of contact points increases. The amount of void space between the beads becomes smaller, reducing the ability of agglomerates to “hide” between the contact points. However, this also results in flow field lethargy. The bead field begins to act more and more as a solid and becomes almostimpenetrable by most slurries. The result is hydraulic packing and plugged screens. Fluidization of the bead field increases the ability of the slurry to flow through it. The higher the degree of fluidization, the faster the slurry makes its pass through the mill and returns for additional passes. The more passes made within a given time period, the faster the dispersion progresses. Hyperactivity of the media field makes aggressive fluidization possible. It is accomplished by dramatically increasing the number of contacts between the media and the feedstock per unit of time thus allowing rapid pass through with high frequency contacts.
CASCADE MILLING MAY NO LONGER BE REQUIRED : (IN SOME INSTANCES)
Hockmeyer developed a design that enables the HCPN mill to take a predispersion to a nano dispersion without plugging the screen. The new HCPN has produced nano dispersions of Methol Violet, Rubine Red, Ultra Transparent Yellow press cake, Phthalo Blue press cake, Crude Blue and many other hard to disperse pigments straight from high speed disperser pre-mix to a nano dispersion in a very short time using .3mm media. No larger media pre-milling was necessary. The conventional wisdom of the need to use media 10 times larger than the largest agglomerate has gone the way of the buggy whip. The reason: Substantially higher power distribution to the bead field, discussed in more detail further on in this paper.
These pigments in some cases, especially the yellow press cake, had agglomerates 1/2 inch in diameter when the milling started, and in a matter of two hours the entire particle size distribution was below the visible wavelength of light. Similar results were obtained in hard to grind solids such as alumina and steel when suspended in the appropriate vehicle.
NO STAGNATION:
When dealing with media small enough to produce a nano dispersion there were other issues in addition to containment that needed to be addressed. For example, the media in the mill chamber must not stagnate at any time in any area. Larger conventional media (above .3mm) is not usually a problem. However, smaller media presents many challenges. As media size decreases, hyperactivity of the flow field becomes paramount.
KINETIC ENERGY DISTRIBUTION IN A HYPERACTIVE BEAD FIELD:
As media gets smaller the mass of individual beads decreases. If the objective is to impact the agglomerates with the same amount of energy generated by the larger media, an increase in velocity is necessary. The kinetic energy of a particle equals one half the particle’s mass times the square of its velocity. Beads are essentially spherical. The volume (and therefore the mass) of a sphere varies with the cube of its radius. So, a small bead ½ the radius of a larger bead will have 1/8th the mass of the larger bead. Because kinetic energy varies with the square of the velocity, the net result is the smaller bead will need 2.8 times the velocity to have the same kinetic energy as the larger bead.
The increase in velocity of individual beads is accomplished by increasing the speed of the impeller assembly. However, it is the counter-peg insert assembly that makes the higher impeller speeds functionally operative. Without it, the higher speeds would merely create centrifuging of the bead field with little effect on milling performance. The combination of these two improvements simultaneously increases flow field activity, bringing it toward the hyperactivity range; the higher the speed, the greater the number of contacts per unit of time and the greater the feedstock throughput.
As the media size decreases the peg tip speed increases to compensate for the loss of mass of the individual beads. Although higher speeds are required to compensate for the reduced mass of small beads, the particles being ground are also smaller, so the kinetic energy per bead does not have to match that of large media.
The net effect is still a higher amount of horsepower per liter of small beads compared to an equal volume of larger beads. Although as beads decrease in size they will continue to break down smaller particles using proportionally less power per bead, the number of beads per liter increases dramatically. The increase in horsepower/liter of beads will manifest itself in higher heat in the bead/slurry field. It will also reduce the amount of time required to reach a given standard, assuming temperature can be controlled within the tolerance range of the slurry. The design of the HCPN mill creates a more uniform power distribution to the bead field thus allowing more power per bead without the heat and wear problems associated with hydraulic packing.
The following is an example based upon power input being equal to power output. Theoretically, to arrive at the same power input/bead on the smaller beads, the horsepower input per liter of beads would have to increase by a multiple commensurate with 2.8 times the velocity increase. However, as the relative mass between the bead and the agglomerate decreases, so does the average power input required per bead to break the smaller agglomerates. Although higher peg tip speeds will clearly require more horsepower (holding bead density as a constant), a number of variables will affect the actual power needed to grind a particular product. These variables include feedstock viscosity, rheology and specific gravity, as well as bead size, density and the types of impellers used to generate flow into and out of the mill. As a general statement, based on Hockmeyer’s laboratory tests to date, a nano immersion mill with small ( at or below .3mm ) media operating at higher peg speeds may require a multiple of as much as two or more times the horsepower of a conventional counter peg mill using large (.8mm and above) media operating at lower peg speeds. What diminishes ongoing de-agglomeration is the reduction in flow field activity as well as the point of diminishing effectiveness of the bead size compared to the particle size. When using very small media, much higher levels of media activity are required to prevent momentary stagnation of the slurry within the flow field and continue the de-agglomeration process. Without this hyperactivity, the process will slow dramatically and further improvement becomes long and arduous. The additional power input via higher peg speeds and increased peg count is required to maintain the hyperactivity in what would otherwise become a lethargic and highly obstructed flow field with little or no throughput of the feedstock in conjunction with rapid temperature rise of the feedstock.
Once the smaller beads have reached equilibrium with the feedstock where the beads are approximately 1,000 times larger than the particles of the feedstock, further particle size reduction will slow to its least efficient level. To continue the particle size reduction smaller media is required. However, our testing of higher peg speeds without changing media size has shown significantly improved performance extending to smaller particle sizes than those generated by the traditionally lower peg speeds. The price for this approach is higher wear to the internal components of the mill.
If bead diameter remains the same but kinetic energy is increased through peg speed, the resulting higher oscillation frequency causes the dispersion to progress further. More frequent collisions coupled with higher relative power/bead compensate for not reducing bead size. Although higher frequency and throughput are of great value, they are not a panacea and will reach a point where bead size must again be reduced for further improvement of the dispersion.
Earlier in this paper a comment was made on how the traditional recommendation of bead diameter to agglomerate diameter ratio of 10 to 1 can be inverted using new technology. Raising and distributing the input horsepower per liter of beads made the process work because of the proportional increase in the amount of energy put into each bead. Without this power distribution addition, inversion of the ratio would not have been possible and the beads would have been unable to overcome the much larger mass they were attacking.
HEAT GENERATION AND REMOVAL:
As the delivered HP/Liter of media increases while the slurry volume remains constant, heat generation increases, becoming yet another obstacle requiring resolution.
Hockmeyer designed a highly efficient heat transfer device for cooling, positioned just below the lower discharge draft tube of the Immersion Mill. Chilled water flows through the device as the bottom propeller surrounded by the lower discharge tube of the mill blows the slurry discharge against, through and around it.
Tests have demonstrated the system’s ability to maintain a temperature of 100 F while the HCPN-1 Immersion Mill was pulling full 10 horsepower in one liter of .3mm ceramic media at elevated peg speeds. The combination of the jacketed tank, the cooled rack dome and the cooling coil, enabled the chiller to remove the heat generated by an introduction of a measured 10 horsepower into the 1-liter media field operating in a 5-gallon batch of pigment dispersion continuously over a 2-hour time period.
BATCH TURNOVER:
Horizontal mill manufacturers typically consider recirculation milling as an increase in throughput that results in about 12 to 16 theoretical turnovers of the batch, occurring over a period of hours. The Immersion Mill can turn the batch over as many as 12 to 16 times per minute and thousands of times during the batch cycle, depending upon the feedstock and its’ cycle time. This produces tighter particle distribution bands and improved qualitative aspects such as color development, transparency, gloss, etc. Utilizing this type of performance from the standard Immersion Mill and coupling it with the ability to run very small media and eliminate cascade milling in many instances, the HCPN has proven to be a substantial step forward in processing technology.
SUMMATION
Nano milling is becoming more and more practical as we learn the idiosyncrasies and demands of the process. The ability to efficiently use smaller and smaller media is an important part of this technology. Equally important, however, are the discoveries of effective media/feedstock separation techniques, the generation of intense and rapid energy exchange between media and feedstock, and the aggressive control of temperature. Understanding and controlling what is actually happening as we engage this frontier is a challenge we continue to embrace and make a reality.