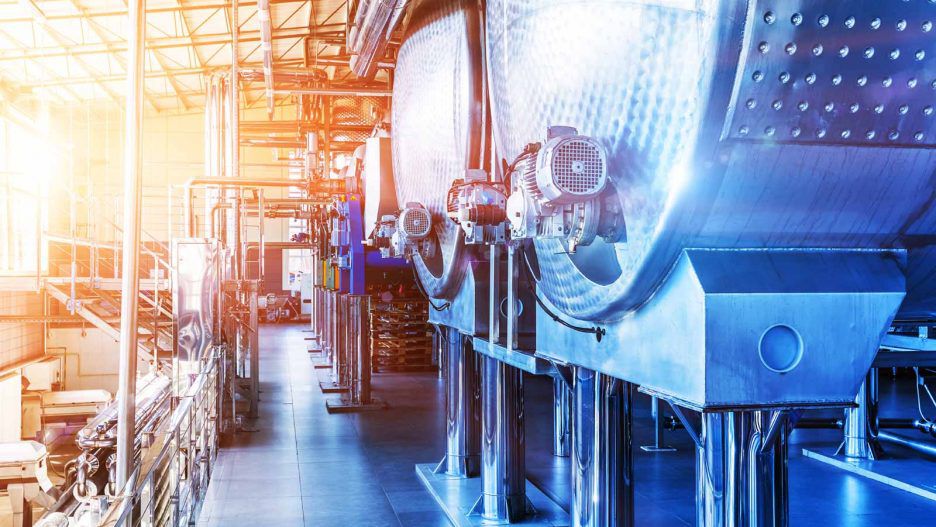
Publications
Shear Forces and Plant Scale-Up
Duplicating dispersion in the factory that has already been successfully achieved in the laboratory can be difficult. Even when the appropriate grind is reached, a 7 Hegman from the factory may not have the same qualitative characteristics as the 7 Hegman produced in the lab. The raw materials all came from the same lots; both dispersions read the same in draw down on the grind gauge. One may be significantly stronger in the tint test. It may even have a gloss difference. To make matters more confusing, the stronger product was done in less time. How can this occur and why? More importantly, what can be done to improve scale-up consistency?
In the interest of accuracy and for the purpose of limiting this discussion we shall address factory scale up in the area of milling, although many similarities are found in mixing as well.
Following are some common areas of inconsistency that can occur between the lab and the factory on a product with identical raw materials and ratios:
- Premix grinds are of different quality
- Media size, density and wear may vary
- Throughput rates/liter of media are different
- Operating temperature of millbase
- Actual power input/liter of media
- Reading a grind gauge can be subjective
- Mill wear
SCALE UP IDEA
One scale up idea explored recently is that of controlling the work input to millbase to ensure that it is constant. Several technical papers have been written on the subject of dispersion at constant power whereby the speed is automatically adjusted to compensate for changes in millbase viscosity. While this offers an improvement on conventional milling techniques because it addresses the power input/liter of media in a fixed time, it can be misleading. The conclusion of scaleup accuracy is somewhat blurred when other important factors are not taken into consideration.
All of the most intricate equations applied to dispersion are useless if the input variables are wrong. Attempting to explain mill performance based upon incorrectly applied design criteria is problematic. Rotational surface area of drive discs or pins correlated to torsional shaft stress may not be the determining factor in performance scale relationship as energy is dissipated through the media field. For example: uniform dwell time and uniform flow field intensity each contributes substantially to the scale characteristics of the finished product yet can be relatively unaffected by the rotational surface area/shaft stress relationship.
MISLEADING CONCLUSIONS
Further complicating the scale problem, the reliance on a grind gauge to support conclusions of quality widens the window of misleading conclusions because an additional, deceptive baseline assessment has been introduced. One could conclude that without correcting for these aspects, scale up inaccuracy is more likely the case. There are numerous other aspects of scale to consider without further complicating the problem by using data measured inaccurately. This practice can only lead to a variety of incorrect conclusions supported by failed reasoning.
Relying upon the use of a grind gauge makes a ‘leap of faith’ to the conclusion that once tiny specs or agglomerates become invisible to the eye below a certain number related area on the gauge, a predictable end result will follow. This is a primitive, vague and misleading measurement of the dispersion, which can be exceptionally expensive in terms of lost quality and profit.
ACCURATE QUALITY CONCLUSIONS
One of the most important aspects of scale up is often overlooked: accurate quality conclusions.
The accuracy of scale in the dispersion process is a function of the accuracy of measure and control of the particle distribution band within a fixed time. The accuracy of measure and control enhance the predictability of the characteristics of the finished product.
Dr. Richard Himics and Ramon Pinero discussed the significance of particle size in dispersion properties in a paper co-authored when they were Colleagues at Daniel Products. They went on to state: “Problems with gloss and durability are usually blamed on the resin used in a coating. Poor strength or hue—as well as other properties such as opacity, transparency or gloss—are often blamed on off-spec pigment.” Many of the problems we experience are not due to chemical reactions or poor raw material quality but only to particle size in the dispersion, a characteristic the raw materials producer and/or the coatings manufacturer can control, given the proper tools.
The following properties are dependent on particle size:
- Hue/Tint Strength
- Gloss/Flatting
- Viscosity
- Hiding/Transparency
- Stability/Settling
- Rub-up/Flocculation
- Weather Resistance.
“The degree to which these properties can be optimized is related to the dispersion process used, the energy expended on the solid particles, and the length of time the pigment particles are subject to the dispersion energy.”
Those who do not have the benefit of particle size distribution analysis or color matching computers employ the use of a simple rub-up test in an attempt to determine if the pigment has fully developed its color potential. “The state of deflocculation of the pigment is related to the particle size; and to obtain optimum results of no rub-up or deflocculation, the pigment must be dispersed to as close to it’s ultimate particle size as possible.”
Differences of 15% and more in strength are not uncommon between a wide distribution band and a narrow one; both reading the same grind on a hand held gauge. Since a significant aspect of the measurement (i.e. the particle distribution band) is not being considered, making assumptions on color strength, gloss, etc, is likely to be incorrect without the use of additional measuring devices. The consequences of poor dispersion are too great.
ACCURATE PARTICLE ANALYSIS
Particle size analysis is an integral part of generating necessary scale up methods. Using a particle analysis system a formulator can expect the quality control and scale up assistance necessary for production accuracy. One can pretest raw materials for quality standards, set formulation guidelines, benchmark production process times to expected particle standards, view reports and document for historical libraries.
The benefit is the ability to scale up and optimize development processes. This structured testing method allows repeatability in the production cycle and accuracy in R&D development.
Laser technology can offer three dimensional particle analyses, which may further enhance accuracy. Both visual and three-dimensional measuring techniques are limited in their ability to accurately measure the size of a non-spherical particle. Most industrial particles measured are not spherical. Our observations have indicated only very minor differences in data generated between the two technologies. However, both offer quantum leaps in product quality predictability compared to a hand held grind gauge.
CORRELATION BETWEEN PARTICLE SIZE AND QUALITIATIVE PROPERTIES
Our research indicates a positive correlation between particle size and qualitative properties of the dispersion. Controlling the dispersion by following a particle distribution band can be challenging. A wide variety of factors can influence the uniformity of the band but for the purpose of this discussion we shall segment into two broad areas and focus on the second.
- Chemical: Instances where particles bond more or less intensely because of the influence of a foreign substance. Example: Coalescing and dispersing agents.
- Mechanical: Instances where particles bond more or less intensely because of the influence of a foreign force. Example: Shear
Energy uniformly applied to a wide particle distribution band tends to narrow and shift the band as a function of time. The largest agglomerates break apart into smaller agglomerates and continue their down-sizing trend until the energy required to make them even smaller is no longer sufficient. An increase in energy input will continue the reduction trend until the next stabilization level is reached.
The continual addition of uniform energy input to the dispersion will challenge the ingenuity of the machinery designer to control the transfer of shear rate into shear stress without exceeding temperature and stress limitations of the dispersion.
Scale should be driven more by the measurable duplication of particle distribution band per unit of time (performance) and the avoidance of subjective variables. Laboratory equipment can be designed to duplicate production equipment using measurable baselines. Machine manufacturers can incorporate the common baseline of particle size distribution into the performance data on dispersion equipment using published, standardized formulas that can become universal performance standards.
Users should be educated in the proper techniques of scale. Equipment manufacturers can focus more on establishing uniform standards of scale and milling consistency rather than impressing users with the performance of a lab mill that cannot be duplicated in the factory. Users should not be left to determine what the manufacturer might have had in mind when the machinery was designed.
In closing, I would urge the standardization of measure via these new technologies will help companies compete in an ever more competitive industry. In particular, the incorporation of particle size analysis as a measure of quality and a basis for scale.