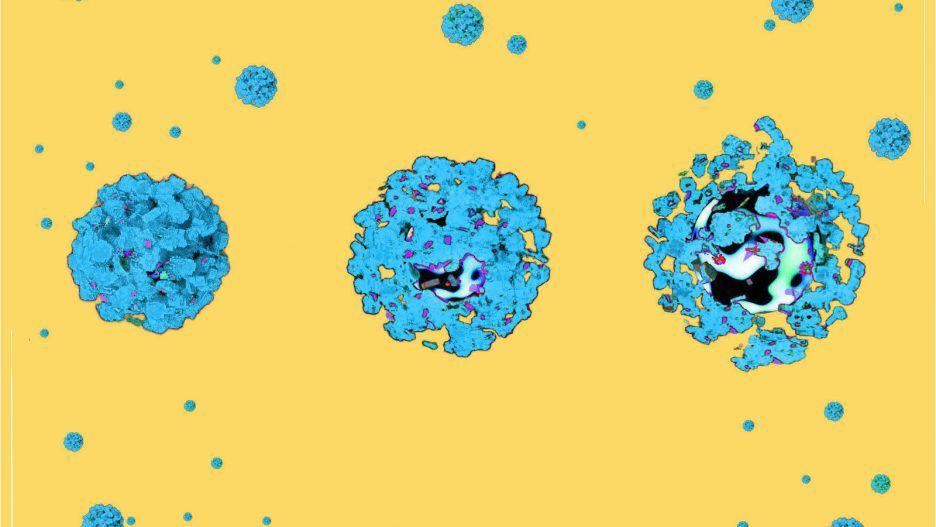
Industry News
Particle Reduction Into the Nanometer Range
As the particle reduction industry continues to make advances, Nanoparticles are becoming key players in the development of new products. These interesting and versatile materials can be found in multiple industries and are changing the characteristics of what was considered “standard. Better, more potent, durable and functional products result in a new world of opportunities never before experienced across a broad spectrum of applications. As these difficult to produce particles enter into more and more consumer and industrial products, manufacturers are left with a growing challenge: How do we produce these particles in an efficient and cost effective manner?
Nanoparticles are produced in two ways “bottom up” or growing Nanoparticles through chemical reaction or “top down” which is producing Nanoparticles by applying mechanical shear to larger agglomerates. In some cases both processes must be used to produces a stable Nanoparticle distribution.
“Top down” particle reduction can be achieved through the use of wet grinding media mills. However, in order to produces these products efficiently, media must be very fine. Media for Nano-grinding can range from 25 – 300 um. This produces unique challenges for both mill manufacturers and their customers. In media milling, media is contained by the mill screen. The smaller the media you use the smaller the screen must be and the more susceptible that screen will be to plugging.
This means that Pre-dispersions for Nano-mills must be very high quality. Manufactures can achieve a high quality premix with several different types of equipment.
- Rotor Stators (when well maintained)
- High Speed Dispersers (when properly configured)
- Pre-milling through a larger media field.
Rotor Stators are very useful tools for applications such as this but are only efficient until the normal wear opens the gap between the rotating and stationary components. High speed dispersers when sized properly, operated at the proper tip speed and equipped with a high shear blade (Hockmeyer D-Blade Recommended) can achieve sufficient pre-grinds in some products. The most efficient way in many cases is to utilize a media mill with larger media (1.5 mm recommended) and a correspondingly larger screen aperture, which allows producers to start the process with larger agglomerates, unsuited for direct Nano-milling. This process must be optimized to provide the best results. All media begins to become inefficient when the particles are smaller than 1/1000th of the media size. This means a 1.5 mm media will become inefficient at 1.5 um. Nano-Mills are most efficient when incoming particle size is smaller than the exit screen and no larger than the media. The target particle distribution for pre-milling would be between 25 um and 100 um. This distribution can often be achieved with a very short pre-mill cycle in a high energy mill.
Equally important is the configuration of the primary (Nano) mill. Hockmeyer has offered a production unit for several years with the ability to produce Nanoparticles. The HCPN Mill provides efficient Nano-grinding, with high end yields and easy operation. The HCPN is built on the current Hockmeyer Immersion Mill platform. This system uses Hockmeyer’s patented bottom prop design to cycle feedstock through the milling chamber and around the tank.
Hockmeyer’s latest patented achievement in particle reduction technology continues to improve the production of nanometer-range particle distributions. Covered under US patent # 8,376,252 B1, this newly designed HCPN Series Immersion Mill can utilize ultrafine media to produce nanoparticles in record times with maximum efficiency. This new design uses an auxiliary chamber that provides a secondary outer wall surrounding the internal media containment wall. Feedstock is passed out of the media field, through the media containment wall and into the auxiliary chamber while the ultrafine media is contained within the mill. It is then pumped out of the auxiliary chamber, with an external pumping mechanism arranged for operation independent of rotation of the rotor, and back into the process vessel for continued recirculation milling. Using this technology we are able to process with media down to .05 mm and achieve particle sizes below 50nm.
As always Hockmeyer’s Customer Testing Facility is open to help you optimize your production process contact us to day to schedule testing. Hockmeyer also offers onsite training to help you get the most out of your existing Hockmeyer Mills.