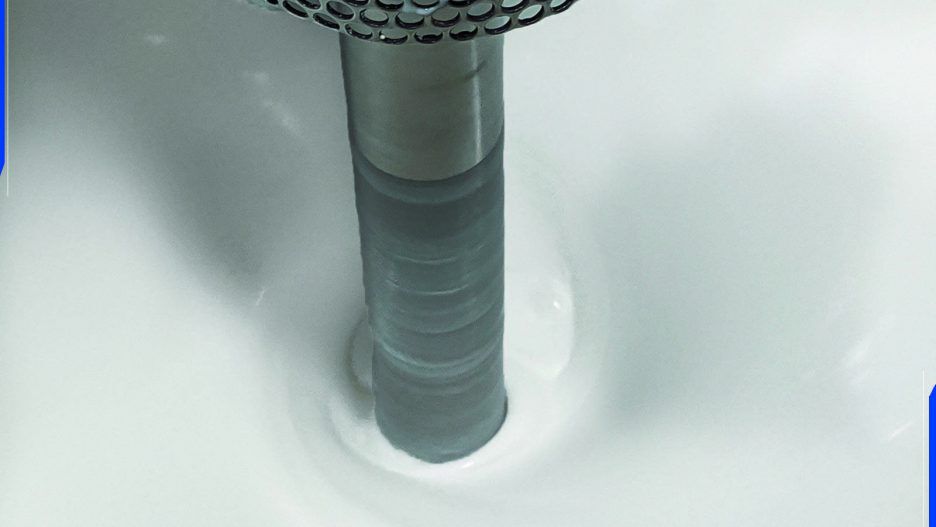
Industry News
Tips for Grinding and Dispersion
One of the keys to proper milling is making a good premix. This is also one of the most neglected processes in the particle reduction industry. The better the dispersion before taking the product over to the mill the more productive the milling cycle will become. Poor premixes cause longer grind times (higher production cost), plugged screens (more down time and product loss) and greater wear on the mill (higher maintenance cost). Reducing these unnecessary costs can return thousands of dollars per year.
There are a few simple rules to making a good premix:
- High particle solids content. Make the dry particle content as high as possible in the premix. Resin and solvents can be added before the mill step. Premix viscosity should create a “donut” shape flow with a small vortex and no splashing.
- Blade diameter should be no less than one third the diameter of the tank.
- Tip speed should be between 5000 and 5200 feet per minute. The formula for tip speed is:FPM = C x rpmC = Л x (D÷12)FPM = Feet per MinuteC = CircumferenceRPM= Revolutions per MinuteD = Diameter in inches(If you cannot reach this speed with the current equipment or formula, then the premix stage is not optimized.)
- Choosing the proper disperser blade is the final step. Hockmeyer offers a wide variety of dispersion blades and can help find the right fit for the process. (Hockmeyer’s patented D-Blade and other blades are available in our lab for trial.)
Good Luck Improving The Process!
Merry Christmas from the Hockmeyer Team!