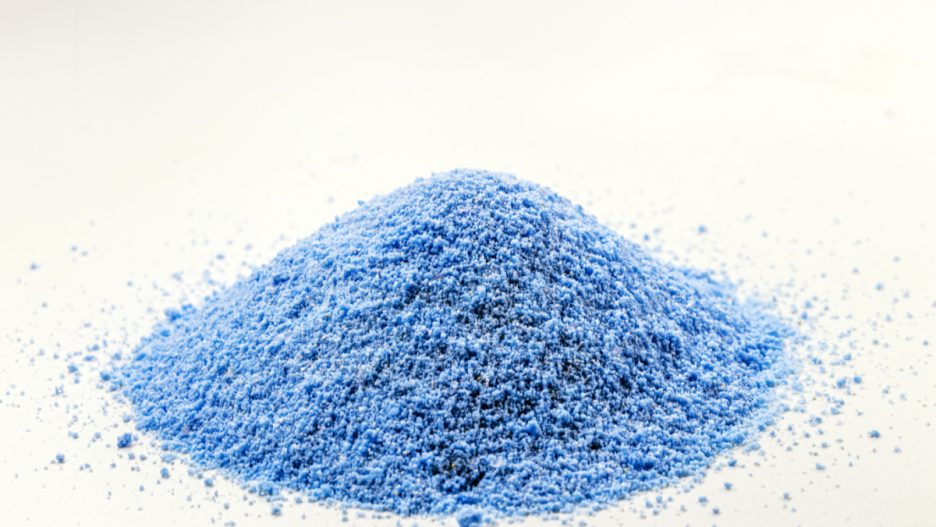
Dispersers and Immersion Mills
Understanding the Importance of Proper Milling in the Final Product Quality
Milling, mixing, and dispersion technologies are used in various industries and applications, from the formulation of paints, coatings, and inks to building materials such as sealants and caulks. They also play a key role in the food, agricultural, cosmetics, and paper industries. Milling even plays a role in the growing renewable energy sector.
In all markets we serve, proper milling plays an essential role in ensuring a consistently high-quality final product. In this post, we will explore particle characterization’s role in product formulation, explain how proper milling helps achieve the desired particle characteristics, and consider how this influences final product quality.
The Role of Particle Characteristics in Product Quality
Particle characteristics refer to the unique and specific attributes possessed by the particles of a particular substance or formulation. The three key particle characteristics that play a role in determining final product quality are size, size distribution, and shape.
Particle Size
Particle size refers to the dimensions of individual particles within a mixture, and the exact size, as well as the uniformity or variation of particle size, can significantly impact the physical properties of a finished product. The size of individual particles can range from nanometers to millimeters, depending on the material, industry, and product requirements.
In applications such as the formulation of coatings, paints, and inks, particle size directly affects the product’s opacity or transparency. Smaller particles often contribute to increased transparency, while larger particles can enhance opacity. In the production of inkjet inks, in particular, maintaining precise control over particle size is crucial for ensuring high-quality print resolution. If particles are too large, they may clog the inkjet nozzles, reducing print sharpness and vibrancy.
In the personal care and color cosmetics spaces, particle size influences a product’s texture, affecting how it feels when applied to the skin or consumed as pills or powders. Fine powders tend to have a smoother application, while larger particles may feel gritty or be more difficult to apply.
In the pharmaceutical industry, controlling particle size ensures proper dissolution and absorption rates, playing a vital role in the medication’s efficacy and safety. Larger particles may dissolve more slowly, affecting the drug’s bioavailability, while smaller particles dissolve faster, potentially improving efficacy.
Particle Size Distribution
Particle size distribution refers to the range and uniformity of particle sizes in a mixture. A narrow particle size distribution means that most particles are of similar size, while a broad distribution indicates a wide range of particle sizes.
In industries such as coatings and agrochemicals, particle size distribution directly affects the product’s flow behavior. A uniform distribution enhances a smooth flow, while a wide distribution can lead to clogging or uneven application.
In products such as coatings or polishing slurries, the size distribution determines the product’s abrasiveness. Irregular or larger particles can cause excessive wear on surfaces, while smaller, uniformly distributed particles offer better performance without causing damage.
In liquid formulations, inconsistent particle size distribution can lead to phase separation or sedimentation. In the production of liquid coatings, in particular, a broad particle size distribution can cause some particles to settle during storage, leading to instability and uneven application when the product is used.
Correct particle size distribution is particularly crucial in products such as pharmaceuticals and paints, where uneven distribution may impact dosage accuracy or application uniformity.
Particle Shape
The shape of individual particles can vary widely, ranging from spherical to angular or irregular. The characteristic of particle shape plays a crucial role in determining how particles interact with one another and how they affect the overall behavior of the finished product.
In particular, irregularly shaped particles can create friction and hinder the smooth flow of a product. This can be particularly important in pharmaceuticals, paints, and coatings. Spherical particles, on the other hand, tend to flow more easily and pack more densely, improving the overall performance of the finished product.
In the conductive slurries used in electronics applications, the shape of the particles can influence the final product’s electrical conductivity. Irregular or angular particles may have a higher contact resistance, reducing the overall effectiveness of the material. Similarly, in structural applications, particle shape can impact the material’s mechanical strength.
In color cosmetics, such as foundation powders, particle shape is critical to achieving even coverage and a smooth application. Irregularly shaped particles may result in a “patchy” finish, while spherical particles provide a more uniform appearance.
Product Behavior and Performance Metrics Influenced by Mixing
All of the factors outlined above play a crucial role in the quality and performance of a finished product. But how can you ensure your particles have the desired characteristics? The answer lies in proper milling and mixing.
Here are just a few key product characteristics, behaviors, and performance metrics influenced by mixing.
Color Strength and Transparency or Opacity
Achieving consistent color strength is vital in applications such as the formulation of paints, coatings, and inks. Proper mixing establishes uniform dispersion of the pigment particles, which affects the final product’s visual properties and performance.
If pigments are not evenly dispersed due to improper mixing, the product may show inconsistencies in color, such as streaks or spots of varying color intensity, when used. In paints and coatings, this can be a serious product defect.
The level of transparency or opacity (how see-through a product is) of a paint, coating, or ink is also controlled by how well the particles are mixed and milled. Large particles not sufficiently broken down or dispersed may create uneven coverage or reduced opacity, damaging the desired aesthetic appeal.
Shelf Life Stability
Shelf life stability refers to how long a product can be kept and still function well when used. Proper milling can significantly extend a product’s shelf life and ensure it remains stable. Proper mixing is essential to guarantee particles remain evenly suspended in a liquid formulation, preventing sedimentation and separation.
In pharmaceuticals, for example, stable suspensions are crucial for ensuring that the dosage remains consistent throughout the product’s shelf life. Proper mixing helps distribute the active ingredients evenly.
In products such as agrochemicals, pharmaceuticals, and food items, poor mixing can lead to sedimentation, where heavier particles settle at the bottom of the container, or phase separation, in which different components of the mixture split apart over time). If you have ever opened a tin of paint to find a layer of oil settled over the top, you have seen product separation.
Agglomeration is also a concern. Without proper mixing, particles may clump together, forming larger agglomerates that affect product consistency and performance. This can drastically reduce shelf life and lead to product recalls.
Flow and Absorption
As we mentioned above, the flowability of a material is influenced by the uniformity of particle size and shape. Proper flow is crucial for easy application and consistent results in various products, including coatings, conductive slurries, and cosmetics. Poor mixing can result in clumps or an uneven flow, making the product difficult to use.
In the case of conductive slurries, which play an important role in electronics manufacturing processes, the flow properties affect the final layer’s uniformity, directly impacting electrical conductivity. Proper mixing allows for even dispersion of the particles, improving the finished product’s overall performance.
In addition, in applications such as pharmaceuticals and cosmetics, particle size and distribution can impact how a material is absorbed by or applied to the body. Poorly mixed products may offer uneven absorption rates, leading to inconsistent performance or effectiveness. In pharmaceutical applications, in particular, this inconsistency could be dangerous.
Other Factors: Conductivity, Abrasiveness, Taste, and Texture
Numerous other product characteristics can also be influenced by proper milling. In this section, we will briefly examine four of them.
Conductivity
For products such as the conductive slurries and inks used in electronics, mixing plays a key role in dispersing particles to maximize electrical conductivity. Clumping or uneven particle distribution can cause electrical resistance, reducing the product’s effectiveness.
Abrasiveness
In applications such as coatings or industrial polishing, particle size and shape affect how abrasive the material is. Proper mixing guarantees that particles are evenly distributed to provide the desired level of abrasiveness without causing undue damage to surfaces.
Taste and Texture
In consumable products such as pharmaceuticals or food items, mixing impacts the taste and texture of the finished article. Inconsistent mixing can lead to unpleasant taste variations or uneven textures, reducing the product’s consumer appeal. In the pharmaceutical industry, poorly mixed powders can lead to uneven dissolution in the body, affecting the drug’s efficacy, taste, and texture.
The Role of Proper Mixing in Achieving Consistent Product Quality
In this section, we will explore how proper mixing plays a role in achieving desired particle characteristics and, ultimately, a consistently high-quality finished product.
Achieving Particle Uniformity Through Mixing
Precision mixing techniques, such as high-shear mixing or dispersing, are essential to achieving uniform particle size and distribution. Advanced milling equipment can break down larger particles into the desired size while ensuring even dispersion throughout the mixture.
Hockmeyer’s advanced dispersing and milling machines are designed to achieve fine, consistent particle sizes. The process guarantees that pigments, fillers, or active ingredients are evenly mixed, producing a uniform product.
In the production of coatings, for example, achieving a precise particle size and distribution is critical for consistent application. Hockmeyer’s equipment is engineered to handle these requirements, ensuring that coatings offer the desired flow and finish.
Reducing Defects and Variability
Product defects can cost a company time and money, as well as have a serious impact on its reputation. In industries such as cosmetics and pharmaceuticals, inconsistent mixing may result in a product that doesn’t meet quality standards, causing rejection or recalls.
Inadequate mixing can result in clumping, poor particle dispersion, or uneven textures. Proper mixing and milling, therefore, plays a crucial role in preventing these defects.
Reducing Variability
Consistency of output is tremendously important to virtually all manufacturers across industries. Variability in mixing can lead to inconsistent product batches, in which one batch may perform differently from another. In the paints and coating industry, for example, poor mixing can result in one batch offering a slightly different color or opacity to another, leading to customer dissatisfaction.
Ensuring Product Stability and Performance
Finally, proper mixing is essential for creating stable slurries, emulsions, or suspensions that remain consistent throughout the product’s shelf life. Adequate mixing prevents phase separation, sedimentation, and ingredient degradation, ensuring the product performs as expected over a long period.
In the agrochemicals industry, for example, maintaining a stable suspension is critical for achieving even distribution and availability of active ingredients when the product is applied. Hockmeyer’s equipment guarantees that these products remain stable, reducing waste and improving efficiency.
Ensure Perfect Milling and Mixing Every Time With Hockmeyer
At Hockmeyer, we have been on the cutting edge of milling and mixing technologies for decades. Our world-class machines are trusted by manufacturers in numerous industries and offer unrivaled control and consistency in determining particle characteristics and ensuring final products are of the highest quality.
We understand that upgrading your mixing technology requires a substantial investment. That’s why prospective clients can try our most popular machines in our state-of-the-art testing laboratory. We will work closely with you to determine the right solution for your needs.
To learn more, contact us, and we will be pleased to help.