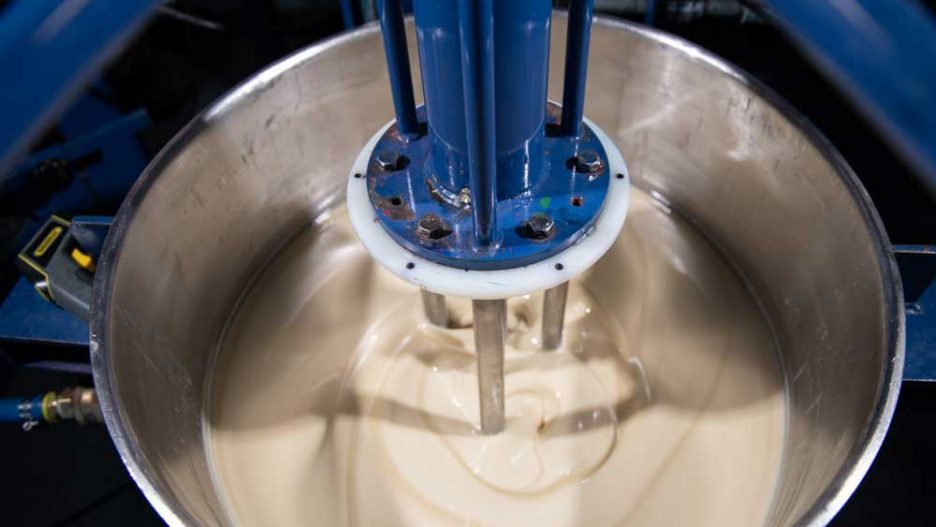
Dispersers and Immersion Mills
Common Challenges in Industrial Mixing and Milling, and How to Overcome Them
In industrial manufacturing, precision and efficiency are paramount. Whether you’re in the printing inks, paints and coatings, agrochemical, or any other industry, achieving the perfect blend or finely milled particles can be the difference between success and failure.
However, common challenges such as long processing times, poor flow, heat generation, wide particle size distribution, and material splashing can hinder production and compromise product quality. Fear not, for with the right approach and equipment, you can overcome these hurdles.
Understanding Industrial Mixing and Milling Challenges
1. Long Processing Times
Time is money, and nowhere is this more evident than in industrial processes. Lengthy processing times delay production schedules and increase operational costs. One of the primary causes of extended processing times is inadequate mixing or milling equipment.
2. Poor Flow
Poor flow within the mixing or milling process can impede the uniform distribution of materials, leading to inconsistencies in the final product. This issue is often made worse by improper machine configuration or blade sizing.
3. Heat Generation
Heat generation during mixing and milling can be detrimental, especially in heat-sensitive materials. Excessive heat can alter the chemical composition of the product or cause unwanted reactions, resulting in subpar quality.
4. Wide Particle Size Distribution
Achieving a narrow particle size distribution is crucial in industries where product uniformity is essential. A wide distribution can lead to variations in product performance, affecting everything from texture to potency.
5. Splashing of Materials
Material splashing not only results in product loss but also poses safety hazards in the workplace. It can lead to equipment damage and create an environment prone to accidents.
Overcoming the Challenges
1. Education/Training
Investing in staff education and training is paramount. Equipment suppliers like Hockmeyer Equipment Corporation offer comprehensive training programs to ensure that operators are well-versed in the intricacies of the equipment, identification and quick replacement of worn parts, and optimal processing parameters.
2. Optimal Machine Configuration
Proper machine configuration will help with many of the challenges mentioned. This includes selecting the right type of immersion milling technology for the specific application and ensuring that it is appropriately sized and configured.
3. Proper Sizing of Blade vs. Tank
The relationship between blade size and tank capacity is critical. An improperly sized blade will lead to inefficiencies in mixing and dispersing, resulting in longer processing times and poor product quality. Additionally, keeping your blades maintained can increase their efficiency and longevity.
4. Height of the Blade Inside the Tank
The positioning of the blade inside the tank affects the efficiency of the mixing or dispersion process. Adjusting the blade height can help optimize performance and mitigate poor flow, which is necessary for efficient processing and homogeneity of the final product.
5. Maintenance Schedules
Regular maintenance will keep equipment running smoothly and prevent unexpected downtime. Establishing a proactive maintenance schedule can help you identify and address potential issues before they escalate, including having the right parts on hand when machinery needs to be maintained.
6. Cleaning Protocols
Maintaining cleanliness is crucial not only for product quality but also for equipment longevity. Implementing proper cleaning protocols ensures that residues do not accumulate, which can lead to contamination or equipment damage.
7. Selection of Screens and Media
Choosing the right screens and media is vital for achieving the desired particle size distribution. Different materials require different media to achieve optimal results, so give careful consideration to selection. Trials at the Hockmeyer lab are available for determining the proper screens and media size for your application.
8. Calculating the Required Horsepower
Determining the required horsepower for mixing or milling equipment is a crucial step in ensuring optimal performance. Factors such as the specific gravity, rheology properties, type, and volume of material being processed, desired processing time, and equipment configuration all play a role in horsepower calculation. Consulting with equipment suppliers like Hockmeyer can help manufacturers accurately assess their horsepower needs and select the appropriate equipment for their operations.
In Conclusion
Although industrial mixing and milling present their fair share of challenges, these challenges are by no means insurmountable. With a combination of proper education, equipment selection, and maintenance practices, manufacturers can overcome these hurdles and achieve the desired results.
By partnering with reputable equipment suppliers like Hockmeyer Equipment Corporation, manufacturers can access the expertise and resources needed to optimize their mixing and milling processes, ultimately driving efficiency and profitability.
If you would like to learn more about how Hockmeyer can help your milling and dispersion pipeline, get in contact with our team of experts. We offer lab testing and support programs to keep your efficiency and profitability on track.