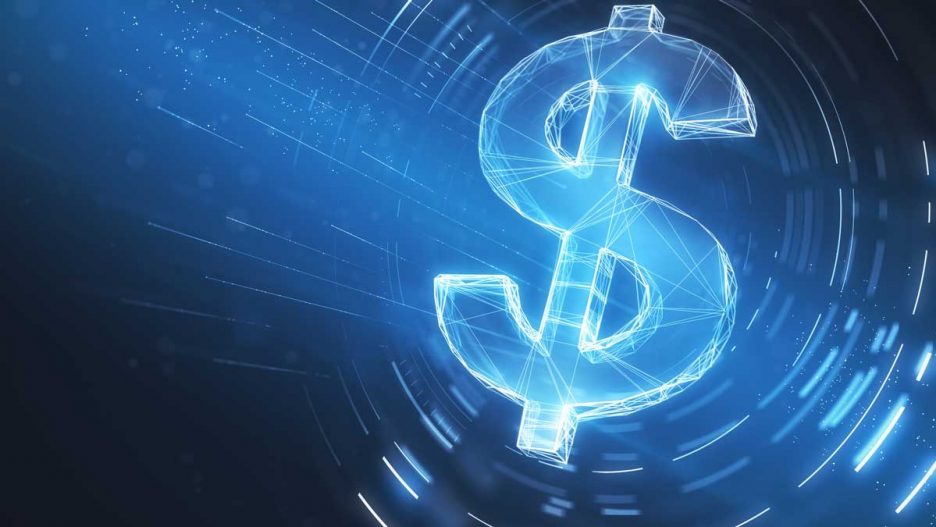
Dispersers and Immersion Mills
Cost-Saving Strategies in Immersion Milling and Dispersion
Most businesses are looking to cut costs and increase efficiency wherever they can, and many opportunities for savings may be overlooked in the immersion milling and dispersion processes. Even if you believe you’ve already streamlined your milling and dispersion procedures, additional aspects of the process may be further improved.
Blade Sizing for Optimal Performance
Selecting the right blade size is crucial in effective milling and mixing processes since the right blade ensures efficient dispersion, minimizes processing time, and reduces energy consumption. Proper blade sizing enhances product quality and consistency, and your tank size and batch quantity directly influence the choice of blade. Matching the blade size to the tank size prevents overworking or underutilizing equipment, and batch quantity impacts the blade’s ability to achieve a thorough and homogeneous dispersion. Incorrect blade sizing can lead to uneven mixing, longer processing times, and increased energy consumption. In contrast, optimal blade sizing contributes to improved and consistent product quality and efficient energy utilization, reducing operational costs and enhancing equipment life span and overall performance.
Horsepower Selection for Product and Batch Size
A motor’s horsepower determines your milling equipment’s energy consumption and performance, so selecting the correct horsepower is essential to prevent overloading or underutilization and ensure optimal efficiency in processing. Appropriate horsepower supports consistent and reliable performance, with alignment to product and batch size helping to avoid unnecessary energy expenditures. Proper matching enhances cost-effectiveness, as excess horsepower can lead to inefficiency and increased electricity costs.
Adequate horsepower not only contributes to the longevity of the equipment but also minimizes operational costs. Inefficient horsepower utilization can increase energy consumption, highlighting the importance of adequately matched horsepower to optimize energy efficiency and reduce the environmental impact. This approach aligns with sustainable and responsible industrial practices by promoting energy-efficient systems.
Regular Equipment Maintenance
Regular maintenance is paramount for preventing equipment breakdowns and ensuring consistent performance. This practice extends the life span of your machines, reducing the frequency of replacements and associated costs. Routine checks contribute to a safer working environment and ensure compliance with industry standards. Essential maintenance tasks, such as lubrication, calibration, and inspection of critical components, play a crucial role in equipment longevity and reliability as well, and regular cleaning to remove accumulated residues prevents performance degradation and enhances overall efficiency. Well-maintained equipment operates more efficiently, requiring less energy for the same output level. Friction reduction, proper alignment, and optimal settings achieved through maintenance contribute to energy savings. Regular maintenance also minimizes unexpected downtime, maximizing operational hours and overall efficiency in industrial settings.
Blade Sharpness and Prompt Replacement of Worn Mill Parts
Sharp blades are indispensable for effectively shearing, dispersing, and milling, as dull blades can increase friction, extend processing times, and decrease overall efficiency. The blades’ sharpness directly influences the final product’s quality and consistency, and indicators of wear, such as reduced efficiency, heightened noise, and uneven processing, should prompt immediate action for blade replacement to prevent deterioration of product quality and minimize energy consumption. In addition to reducing processing time and saving energy and operational costs, sharp blades contribute to efficient shear, lowering wear on other components and minimizing the need for frequent replacements.
Regular inspections are crucial for identifying worn components, including blades, pegs, screens, seals, bearings, and belts. Monitoring for unusual sounds, vibrations, or leaks is an early warning system for potential wear and tear, and tracking performance metrics further assists in pinpointing parts that may need replacement. Unexpected breakdowns can be prevented by establishing a proactive replacement schedule based on wear indicators and manufacturer guidelines, and by promptly replacing worn parts, you can minimize the risk of secondary damage to other components. Timely replacement of worn parts sustains equipment efficiency, preventing a decline in performance. This proactive maintenance approach reduces the risk of unplanned downtime, contributing to your overall operational efficiency and extending the life span of your equipment.
Balancing Solids Percentage and Viscosity
Achieving the right balance between solids percentage and viscosity is crucial for optimal milling. This balance influences material flow and consumable parts’ wear, affecting the efficiency of the process. Maintaining it ensures maximum efficiency and consistent product quality. Thorough material testing guides adjustments in formulations and process parameters, and regular monitoring and fine-tuning based on variations and production needs are vital. Efficient milling and dispersing rely on carefully controlled solids percentage and viscosity, highlighting the importance of precision in material characteristics for successful operations.
Milling for Maximum Color Development
Milling directly influences the finished product quality and color intensity. Efficient milling processes are critical to achieving thorough dispersion, maximizing the particle deagglomeration and grind to achieve optimal color development. The level of efficiency and pigment development can influence the product’s market competitiveness by realizing raw material cost savings and reducing processing times.
Start Saving With New Solutions in Milling, Dispersing, and Mixing
No matter what your needs are, our immersion milling and industrial mixing solutions can help you achieve the results you’re looking for. If you’re interested in learning more, we’re ready to help and look forward to hearing from you! Contact us today, or learn more about our product testing lab.