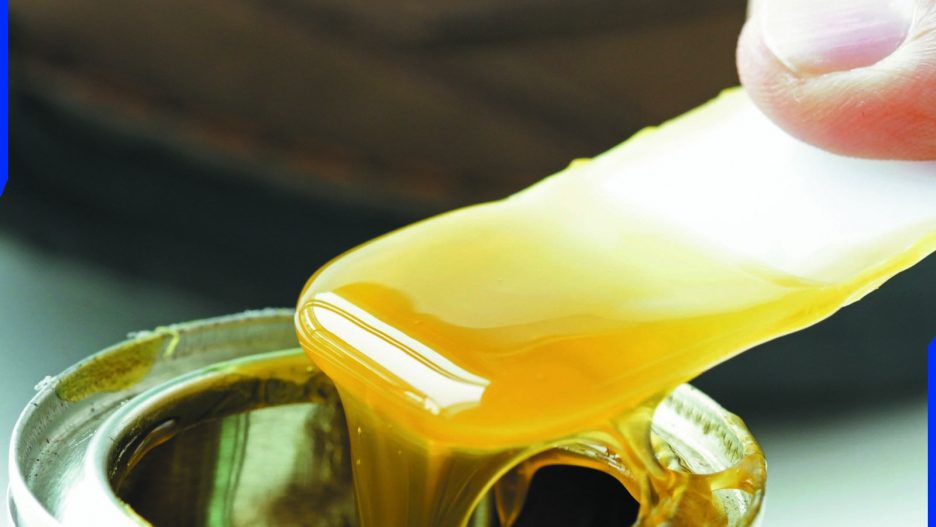
Industry News
Producing Adhesives Under Vacuum
Adhesives continue to evolve as one of the key building materials multiple industries. As adhesives improve demand goes up and manufactures must find new ways to process quality adhesives in an efficient way.
Adhesives are often produced by blending melted polymers or by dissolving polymers into organic solvents. In both of these approaches one of the primary problems is the incorporation of air. Most adhesives have a high surface tension that makes removal of air, once it is incorporated through mixing, difficult and time consuming. Excess air in a product can effect everything from packaging to performance. Due to this, most adhesive manufactures have shied away from high shear mixing in favor of low energy agitators, which do not incorporate air, but can take significant amounts of time to dissolve or melt polymers.
For adhesive formulations that can handle high shear there is a way to prevent this. Processing adhesives under vacuum from start to finish will prevent air incorporation regardless of how aggressive the blending process becomes. This can result in huge savings for manufactures. While simply processing under vacuum is enough to eliminate air incorporation it is not the whole solution. The configuration of the equipment is also critical to reducing the process time. Hockmeyer’s Dual and Triple Shaft Mixers are ideally suited to this goal. The helical sweep blade provides excellent product movement and our patented bidirectional trailing scraper design provides unparalleled heat transfer and the rapid incorporation of raw materials. This, along with multiple shear options: high shear blades, rotor stators, augers and even the Immersion Mill, can drastically reduce the time required to produce a quality air free adhesive.
Hockmeyer’s Customer testing facility has vacuum capable Dual and Multi-shaft Mixers available for testing from 2 to 35 gallons. Schedule a test today to find out how much we can reduce your process time!