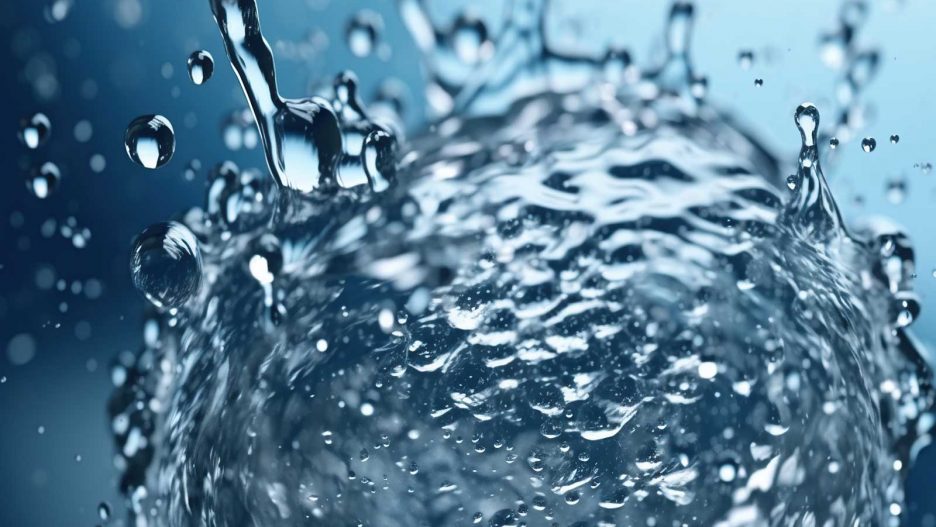
Dispersers and Immersion Mills
Optimizing the Industrial-Tank-Washing Process
Efficient tank washing is critical in industrial milling and manufacturing, offering benefits, including improved efficiency, reduced chemical usage, and minimized waste. Streamlining the tank-cleaning process allows team members to be reassigned to other tasks, enhancing overall operational productivity. When executed effectively, tank washing has the potential to be an overlooked profit center, making this aspect of industrial operations one that should be at the top of your list to optimize.
Test Various Detergents and Solvents
Choosing the appropriate solvent for industrial tank cleaning is crucial, thanks to the diverse range of residues and contaminants involved. Using a less-than-suitable solvent may lead to missed opportunities for excellent results, and factors such as temperature, pressure, and the compatibility of cleaning agents with tank materials also impact the effectiveness of the tank cleaning and prevent equipment damage.
Thorough testing ensures optimal performance in real-world scenarios and addresses environmental considerations, including sustainability goals, minimizing waste, and meeting regulatory requirements. It also emphasizes the importance of selecting eco-friendly and biodegradable solutions in the cleaning process.
Understanding Brush Configurations
The significance of brush configurations in tank washing is incredibly impactful, as these configurations play a pivotal role in determining cleaning effectiveness for tanks of various shapes and sizes and equally diverse residues. Different brush types offer versatility, influencing factors such as cleaning coverage, the ability to reach difficult areas, and the wear and tear of tank equipment through multiple uses.
While some tanks may use premade brushes, exploring custom-made configurations may be necessary to give you the results you’re looking for because factors like bristle material, stiffness, and shape are all essential for optimal performance. Overall, varied brush configurations provide flexibility, allowing you to adapt your tank-washing strategy to evolving needs and challenges.
Proper Planning Is Key
Efficient planning is crucial for effective tank washing. Like dishes washed after a meal, immediate cleaning is essential to prevent materials from settling and becoming more challenging to remove. Develop a comprehensive schedule aligning tank cleaning with production cycles and planned downtime, integrating it into routine maintenance to ensure consistent cleanliness and prevent unexpected disruptions.
To accomplish this, allocate adequate resources, including manpower, cleaning agents, and equipment, tailored to each tank’s specific requirements and employ advanced technology and automation for enhanced resource efficiency. Implementing a proper staging area that facilitates continuous tank washing and streamlined processes for moving tanks to and from the production line will also allow you to maximize overall efficiency and boost your profits.
The Importance of Your Quality Control Process
Quality control is critical to ensuring the effectiveness of the tank-washing process in removing residues and contaminants. Regular inspections help to verify that cleaning agents and equipment achieve the desired cleanliness, preventing equipment corrosion and deterioration caused by lingering residues.
These quality control measures assist with identifying and addressing issues early on, including potential risks like equipment malfunctions, inadequate cleaning, or safety hazards associated with tank washing.
Hockmeyer’s CMX-200 Vessel Washer
The Hockmeyer CMX-200 stands out for its efficient cleaning capabilities suitable for tanks and drums of varying sizes. Crafted with robust steel construction, this machine incorporates dual high-pressure hydraulic hoists designed for effortless machine elevation and descent on recirculating ball bearing guides. The rotating brush and spray nozzle assembly deliver a powerful combination of mechanical scrubbing and soaking action, ensuring effective cleaning of your vessels. Many competitors use only a high-pressure nozzle without brushes, which is adequate for some products but can cause challenges with others once they’ve dried on the vessel. This combination of nozzle and brush paired with proper planning and cleaning materials can allow over 20 tanks to be positioned, soaked, washed, rinsed, drained, and moved per 8-hour shift. Average wash cycles run between 5 & 15 minutes, dramatically reducing the required time from manual tank cleaning.
Other standout features include a baseline tilting assembly for efficient drainage, a choice between Polyethylene or Teflon lid liner construction, and the availability of custom brush assemblies tailored for special applications. This innovative design enhances productivity and increases profitability by optimizing the cleaning process. Additionally, the CMX-200 features a closed system during operation, effectively controlling solvent vapors and handling hazardous compounds, prioritizing safety and environmental considerations in industrial settings.
Ready to Learn More?
If you’re prepared to leverage the benefits of the CMX-200 in your manufacturing facility, we’re here to guide you through the sometimes confusing process of assessing your needs and can answer any tank-washing questions. Contact us today to learn more and for customized insights into how the CMX-200 can enhance your operations and bring about efficiency.
Our dedicated customer service team is ready to assist you at every step, and our support extends beyond initial inquiries, offering comprehensive testing services to give you all of the information (and peace of mind) you need. Whether you want to find out if the CMX-200 is the right fit for your business or want to test samples of materials to determine the best tank-washing configuration for a specific job, Hockmeyer is equipped to provide the solutions you need.