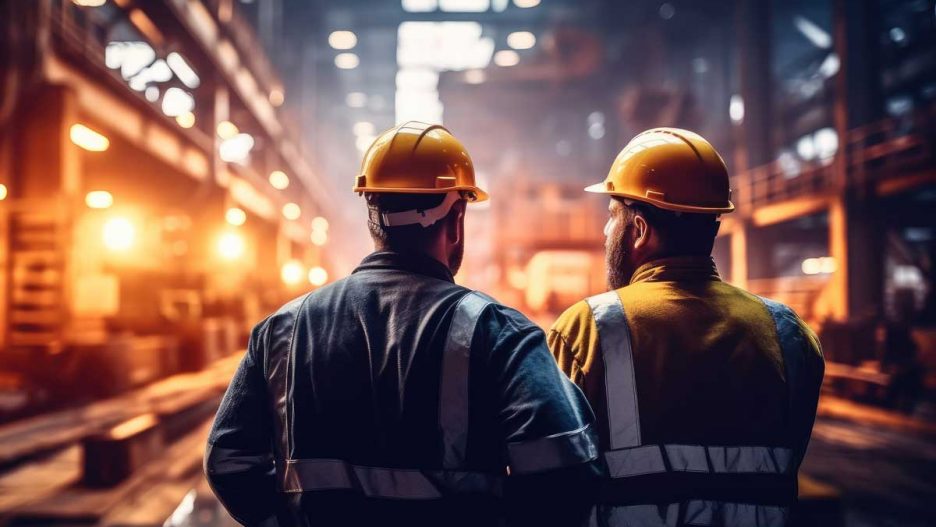
Dispersers and Immersion Mills
Safety Measures in Industrial Mixing and Milling: Protecting Personnel and Equipment
Each workplace has hazards, and industrial mixing and milling facilities are no exception. Dangerous conditions can arise quickly if left unchecked, which is why staying on top of important precautions is essential to ensuring the safety of your business’s personnel and its equipment. To avoid future challenges, it’s first necessary to understand the risks that come with the industry and what measures can be taken to mitigate them.
Common Hazards in Industrial Mixing and Milling
Workers face various hazards during the industrial mixing and milling processes that require careful consideration to ensure workplace safety. Chemical exposure poses a significant risk since workers may come into contact with potentially harmful substances during the workday. Mechanical hazards are also important to consider since the operation of machinery and equipment can lead to injuries if not handled properly.
Additionally, noise and vibration in these environments can contribute to long-term health issues for workers. Dust and particulate matter further add to the list of hazards, posing respiratory threats and requiring appropriate protective measures to address the risks associated with these industrial processes. Employers must implement comprehensive safety protocols to address all of these common hazards and prioritize the well-being of their workforce.
Machine Safety
Proper electrical grounding is essential for maintaining a safe working environment and addresses multiple aspects of electrical safety. The primary goal of grounding is to prevent electric shocks; this is achieved by ensuring that electrical currents have a low-resistance path to the ground, which significantly reduces risk to employees. Grounding also plays a crucial role in equipment protection: It safeguards machines and equipment from electrical faults, such as short circuits, by providing a pathway for fault currents to flow safely to the ground while preventing damage and minimizing downtime. Additionally, grounding contributes to fire prevention by limiting the accumulation of excess voltage in the presence of faulty wiring or electrical malfunctions, which reduces the risk of overheating and
electrical fires. In environments where static electricity is a concern, proper grounding dissipates static charges, mitigating the risk of sparks that could ignite flammable materials or cause explosions.
Ensuring the safe anchoring of tanks is also paramount in industrial settings as an important measure to prevent accidents and injuries. Proper anchoring plays a vital role in maintaining the stability of tanks, reducing their risk of tipping over or shifting during operation. This stability is essential during high-speed milling or mixing processes, ensuring the equipment operates smoothly without unexpected movements. This preventive approach safeguards against environmental contamination and creates a secure working environment for personnel involved in industrial processes.
Safety measures are crucial for protecting personnel and ensuring efficient mixing and milling, especially when machinery isn’t in use. Installing guards around the mixer blades when not in use protects operators by preventing accidental contact with the blades. Beyond safety considerations, efficient mixing blades are crucial to minimizing dust and emissions during operation; this safeguards the health of personnel, as exposure to airborne particulates poses respiratory and overall health risks. Additionally, using effective mixing blades reduces the need for manual intervention to address uneven mixtures, lowering the risk of injuries. Well-designed mixing blades also contribute to the prevention of material buildup on the mixing vessel’s walls, ensuring a consistent and safe mixing process by avoiding potential blockages. Collectively, these safety and operational considerations create a secure and efficient working environment.
Personnel and Employee Safety
Ensuring personnel and employee welfare in industrial settings involves a multifaceted approach that highlights various key elements. Proper maintenance of machinery is fundamental to equipment reliability and contributes to the overall safety of personnel. Proper training is crucial, especially considering that operating procedures may evolve with new machines or improved procedures. Enforcing clothing standards around mixers can also help avoid safety liabilities such as hang tags that could cause harm if caught.
Additionally, proper personal protective equipment (PPE), including gloves and masks, is essential to reduce the risk of exposure to chemicals and solvents. Emergency response planning is also vital and emphasizes the importance of having a well-defined plan can help minimize the impact of any issues that may arise; this can include knowledge of first aid locations, designated communication channels with first responders, and clear responsibilities for organizing and adhering to emergency procedures. This
comprehensive approach will go a long way toward creating a safe working environment and preparedness for potential emergencies.
Incorporating a Tank Washer
Tank washers offer a range of features specifically designed to enhance the cleaning process, mainly when manual cleaning isn’t feasible. These features often include automated cleaning cycles, emergency stop functions, and safety interlocks, providing added layers of protection to prevent accidents during operation. Some tank washers, like Hockmeyer’s own CMX-200, provide a closed system during operation to control solvent vapors and the handling of hazardous compounds. By incorporating these safety-oriented features, machine tank washers can contribute to a safer working environment.
One notable advantage of tank washers is their capacity to reduce workers’ exposure to solvents and cleaning agents. Manual tank cleaning typically involves direct contact with these potentially hazardous chemicals, exposing workers to risks such as skin irritation and respiratory issues. With machine tank washers, the need for direct contact is minimized, thereby lowering the risk of health hazards related to chemical exposure. Additionally, automated tank washers operate with precision, reducing the potential for spills compared to manual cleaning methods. This precision prevents accidental spills, which can lead to slip hazards and environmental contamination and pose risks to workers’ safety.
Furthermore, tank washers contribute to improved air quality by minimizing the release of airborne particles and vapors during the cleaning process, thereby helping protect workers’ respiratory health. Automated tank washers’ consistent and thorough cleaning performance further ensures the removal of residues and contaminants, reducing the risk of inadequate cleaning and potential safety compromises in subsequent processes.
Best Practices for Ensuring Safety
Implementing best practices can help create a robust safety culture for your employees. One essential practice is having leadership establish this culture by playing a crucial role in actively demonstrating and communicating their commitment to safety, setting a tone that permeates the entire organization. Encouraging employee participation in safety initiatives is equally important, fostering a sense of ownership and responsibility for creating a safe work environment. Regular audits can assess the effectiveness of protective measures and identify improvement areas. Documenting findings and establishing a systematic reporting process provides a reference for tracking progress and addressing identified issues. Engaging external professionals or auditors adds an unbiased perspective to evaluating safety practices and compliance.
Continuous improvement in safety protocols is another vital aspect of best practices. Analyzing incident reports, near misses, and audit findings helps identify patterns and improvement areas. Organizations should compare safety performance with industry benchmarks and best practices, adopting proven strategies from other entities to enhance protective measures. Embracing technological advancements, such as sensors, monitoring systems, and predictive analytics, contributes to identifying potential risks. Encouraging employee feedback and reporting is also a great way to improve, as establishing open communication channels where employees feel comfortable reporting concerns without fear of reprisal is crucial. Implementing a system that recognizes and rewards employees for contributing to improvements through reporting or suggesting enhancements further reinforces a proactive safety culture. Ensuring employees are educated on reporting procedures and conducting regular feedback sessions to update them on the outcomes of reported concerns and actions taken enhances safety awareness and responsiveness.
Improve Your Safety Practices With Hockmeyer
If you’re interested in learning more about how solutions from Hockmeyer can assist you in making your facility safer and more efficient, our team is ready to help. Our support continues through your initial inquiry and beyond, with offerings for comprehensive testing services to give you all the information (and peace of mind) you need. Our team can also provide Field Training and Support to ensure your plant’s safety. Whether you want to find out if tank-washing solutions like the CMX-200 are the right fit for your business or would like to explore how our team can help you make your facilities the safest they can be, we’re here to provide the solutions you need.