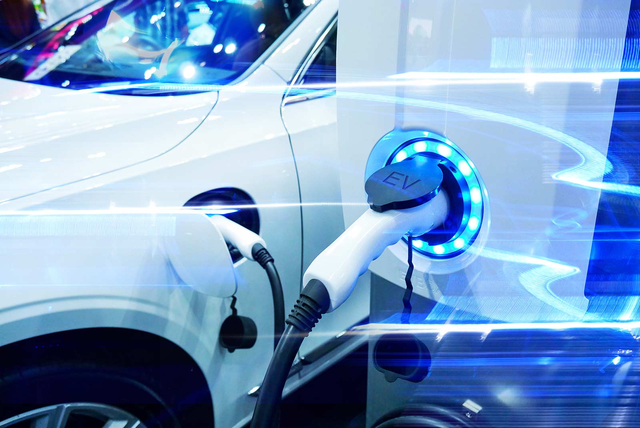
Dispersers and Immersion Mills
The Role of Particle Size in Battery Cathode and Anode Slurries
Rechargeable lithium-ion batteries are expected to be a critical player in making transportation more sustainable through battery-powered electric vehicles. However, the battery manufacturing process has its own set of challenges that must be addressed. As we continue to work toward a sustainable future, immersion milling technology has the power to improve the quality of raw materials used in the battery manufacturing process, shorten process times, and make those essential changes a reality.
Why Battery Manufacturing Is Important for Sustainable Energy
While they are not a new technology, batteries are a tool that can assist with society’s transition from heavy reliance on fossil fuels to more sustainable options. And with the rise of electric vehicles (EVs) and the need for energy storage, batteries have seen a massive uptick in development, which has created its own set of sustainability challenges as the market continues to grow exponentially. The solution to these challenges cannot simply be found by addressing one aspect of a battery’s life cycle; it must instead lead to changes at every stage, from the battery’s design and the development of raw materials through the manufacturing process and beyond.
How Do Batteries Work?
Batteries store chemical energy and convert it to electrical energy through components called electrodes, which help create the flow of electrons that generate the required electrical energy. The electrodes are separated by an electrolyte, which can be either a liquid solution or a solid, and a battery’s efficiency depends on which materials are used for these components and how well they are processed.
Lithium-ion batteries are widely used in portable electronics and electric vehicles because they are rechargeable and can store more energy in a smaller space relative to other batteries, but they do pose their own manufacturing and sustainability challenges. For example, the electrolytes used in lithium-ion batteries are typically a metal oxide or a graphite, and they are delicate materials requiring sophisticated manufacturing methods and quality controls. The production of lithium-ion batteries also involves raw materials that are difficult to access and require complex extraction processes.
How Can Dispersion and Milling Enhance the Battery Manufacturing Process?
Particle size reduction and dispersion are essential steps in the processing of components for battery manufacturing. Battery manufacturers apply electrode materials as a slurry to form a film, and the size and shape of particles within slurries are critical to the uniformity of the film and its final quality. In a battery slurry, the need for precise processing requires a specific rheological profile, meaning that viscosity and shear thinning properties must be carefully controlled. Agglomeration and poor particle size distribution can cause difficulties in the coating process, which will create film uniformity issues that can negatively impact the ion transfer rate and recharge cycle time of the battery.
To avoid these issues and ensure improved battery performance, the manufacturing process must provide greater control over the materials used and their physical properties, including the particle size distribution. Reducing the particle size will increase the specific surface area, improving important battery characteristics, but a reduced particle size also changes the size of the voids between electrode particles and can decrease battery capacity, so it requires a careful balance.
Dispersion and Milling Solutions From Hockmeyer
The equipment used during the processing of the slurry for the final battery manufacturing process makes all the difference in ensuring the quality of the final product. Through innovative mixing, dispersing, and milling solutions, it is possible to make slurries for battery manufacturing more efficient, consistent, and reliable to ensure the creation of effective batteries.
HVI Hoist Mounted Disperser
The HVI Hoist Mounted Disperser is a variable-speed, single-shaft mixer/disperser that features exclusive high-pressure with no 0-packing maintenance when compared with low-pressure lifts. This disperser is environmentally friendly thanks to its leak-free performance, which ensures no oil leaks, mist, or seepage and up to 85% less oil usage.
Hockmeyer HCP Immersion Mill
The Hockmeyer HCP Immersion Mill uses rapid recirculation milling technology to efficiently achieve a homogeneous batch and reach the required particle size and particle distribution. This is achieved by recirculating the slurry through the chamber repeatedly—as many as 50 batch turnovers per hour with an accurately paired mill and tank. Benefits of this mill include reduction of process time, tighter particle size distribution, reduction of raw material costs by maximizing development, and minimal product loss with thorough and efficient cleanup, which also make this mill an environmentally friendly option.
NEXGEN™ Vacuum Recirculation Mill
Utilizing revolutionary, patented technology in the field of particle size reduction, the NEXGEN™ Vacuum Recirculation Mill uses vacuum force to remove air and deagglomerate particles. The removal of microbubbles maximizes media performance, resulting in a purer, faster, and more efficient grind. The distinctive design of this mill allows the use of the smallest grinding media available for nano-milling. It often achieves results in half the time of its horizontal milling counterparts, and the cost of raw materials can be reduced greatly by maximizing development.
Interested in Learning More?
No matter what your needs are, our wide variety of solutions can help you achieve the results you’re looking for. If you’re interested in learning more about the milling solutions we offer at Hockmeyer to further improve and streamline the battery manufacturing process, we’re ready to help. Contact us for more information about our products and how they can best serve you and your needs. Our knowledgeable team is ready to assist you as you work to streamline your company’s milling process, and we will find the equipment that you need to maximize your operations.