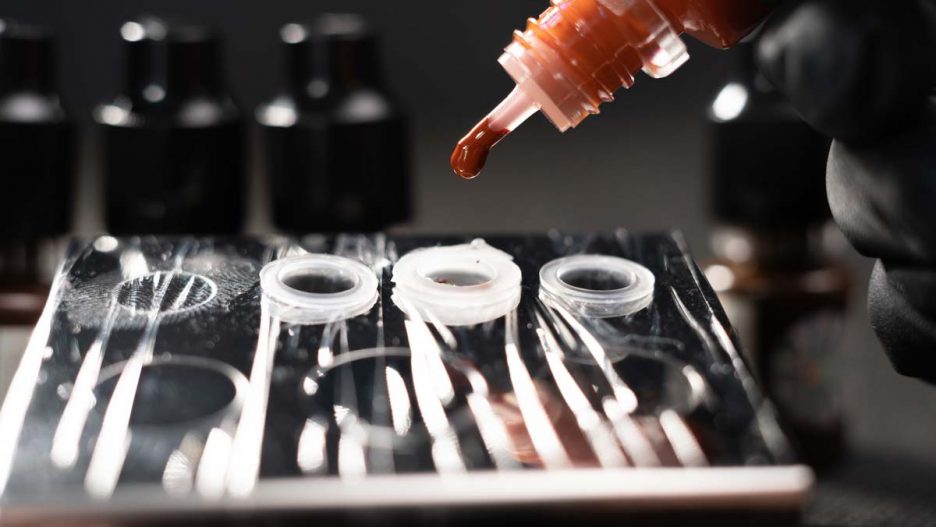
Dispersers and Immersion Mills
How Proper Milling Techniques Increase Pigment Yield
High pigment yields are key for many products, not only for economic considerations but also because they serve as a barometer of quality and efficiency. Proper milling techniques and innovative milling equipment are essential for optimizing pigment yield, resulting in cost reduction and elevating color intensity, durability, and overall performance of the pigments, reinforcing the integral relationship between quality and efficiency.
Understanding Pigment Dispersion
Understanding the concept of pigment dispersion is of utmost importance, since pigment dispersion is essential for achieving vibrant and consistent colors in products like paints, inks, and paper coatings. The dispersion process requires disassembling pigment agglomerates into individual particles and evenly distributing them. Ineffectual dispersion can result in issues such as inadequate color development, reduced hiding power, subpar film appearance, and diminished durability. The key isn’t just increasing pigment content in a formulation; it’s about ensuring each pigment particle is thoroughly and stably dispersed within the mix, guaranteeing the desired quality and performance in the final product.
Why Proper Milling Techniques Increase Pigment Yield
Proper milling techniques are pivotal in achieving effective pigment dispersion, a critical aspect in various industries. The milling process involves the reduction of pigment particle size, breaking down agglomerates, and attaining the desired fineness to enhance color development and ensure consistent gloss and other essential properties. Particle size reduction, a primary outcome of milling, leads to smaller particles that provide a greater surface area for interaction with binders and other additives, resulting in improved color development and the efficient use of pigments. Moreover, the breakdown of pigment agglomerates into individual particles through proper milling ensures a uniform dispersion throughout the paint matrix, which, in turn, enhances hiding power—the paint’s ability to effectively cover the underlying surface.
Effective pigment dispersion further improves color consistency, as milling minimizes variations between batches, ensuring the desired color is accurately reproduced each time. This consistency is highly important in meeting the expectations of clients who demand uniform results. Additionally, milling contributes to the smoothness and evenness of the film, enhancing its overall appearance and providing a more professional finish. Notably, this process also increases the durability of the final product, as properly dispersed pigments are more resistant to fading, cracking, and other environmental influences, ensuring a longer-lasting and higher-quality result.
How to Choose the Right Milling Technique
Streamlining the milling process requires understanding the complexities of pigment dispersion and several critical factors. Firstly, the type of pigment you are working with plays a fundamental role in the process. Different pigments exhibit varying degrees of hardness and agglomeration tendencies, making it essential to understand their specific characteristics before choosing the appropriate milling method. Another crucial factor to consider is the compatibility of the chosen milling technique with the binder system in use. Some milling processes may be more compatible with certain binders than others, ensuring a harmonious integration of pigments into the overall formulation. Additionally, the desired particle size for your application significantly influences the choice of milling technique. For instance, bead mills can achieve finer particle sizes than ball mills, offering versatility in meeting specific particle size requirements.
In the decision-making process for selecting a milling technique, assessing practical aspects is vital. Factors such as production scale, required throughput, economic considerations, and environmental and safety factors should be evaluated. The production scale and desired throughput should align with the chosen technique, ensuring it’s suitable for large-scale industrial settings or smaller laboratory applications. Moreover, economic factors, including the cost of milling equipment, energy consumption, and maintenance requirements, should be considered to ensure long-term cost-effectiveness. Lastly, environmental and safety considerations come into play, as some milling techniques may generate more waste or involve the use of hazardous materials. It’s imperative to consider these factors while ensuring compliance with safety and environmental regulations throughout the pigment dispersion process.
Ready to Learn More?
Selecting the best equipment for your manufacturing process requires a thorough assessment of how it aligns with the unique characteristics of your products. Your new equipment should seamlessly integrate
into your existing process or, ideally, streamline it by eliminating any unnecessary steps. Various factors come into play when making this decision, including considerations like processing time, scalability, ease of cleaning, product preservation, ergonomic factors, and the equipment’s capacity to meet or exceed your standards.
Recognizing the complexities of this decision-making process, we have equipped our Customer Service and Testing Facility with laboratory, pilot, and production models of our equipment. Initial testing is always free, simplifying the evaluation and selection process for your new equipment. If you’re interested in learning more, contact us today. Our expert service and sales teams are ready to assist you and demonstrate how Hockmeyer technology can make a difference for you.