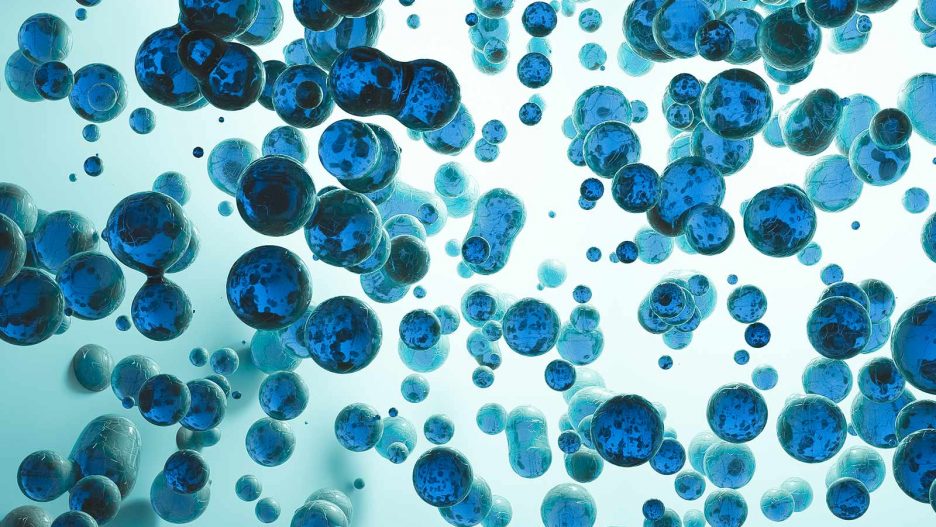
Industry Information
How the Nano Milling Process Works
With continued advances in the milling and particle reduction industries, nanoparticles are now key players in the development of new products. As these versatile materials become integrated into a variety of consumer and industrial materials, the results speak for themselves: more potent, durable, and functional products that lead to a whole host of new applications and opportunities for nanoparticles.
However, thanks to the complicated process required to create nanoparticles, manufacturers are left wondering how these particles can be produced efficiently and cost-effectively. Thankfully, progress is being made in adjusting to the challenges and demands of the nano milling process.
What Are Nanoparticles, and How Are They Produced?
Nanoparticles are an ultrafine piece of material with dimensions measured in nanometers. These particles exist naturally but are also produced in two ways as a result of human activity: either “bottom-up” (growing nanoparticles through chemical reaction) or “top-down” (producing nanoparticles by applying mechanical shear to larger agglomerates), otherwise known as nano milling. These particles are invisible to the naked human eye, and thanks to their submicroscopic size, they have unique characteristics applicable to a variety of applications in a wide range of industries.
The process of nano milling, or nano grinding, is the reduction of particles down to a very fine consistency through the use of wet grinding media mills. Reducing particles to sub-micron size presents unique challenges because the smaller the media you use, the smaller the mill screen needs to be, and the more susceptible that screen is to plugging. To avoid problems like plugged screens during the milling process, pre-dispersions for nano milling need to be of the highest quality, which can be achieved through several types of equipment, including well-maintained rotor stators, properly configured high-speed dispersers, and pre-milling through a larger media field.
Rotor stators can be useful tools for nano milling applications; however, they are efficient only until the normal wear and tear on the machine increases the size of the gap between the rotating and stationary components. When sized properly, operated at the proper speed, and equipped with a high-shear blade like the Hockmeyer D-Blade, high-speed dispersers can also achieve sufficient pre-grinds in some products. Still, in many cases, the most efficient way to reduce materials to the desired proportions is to utilize a media mill with larger media (1.5 mm recommended) and a correspondingly larger screen that allows producers to begin the milling process with larger agglomerates, unsuited for direct nano milling. Nano mills are most efficient when the incoming particle size is smaller than the exit screen and no larger than the media. This means that the target particle distribution for pre-milling should be between 25 um and 100 um, a distribution that can often be achieved with a very short pre-mill cycle in a high-energy mill.
The HCPN Immersion Mill and NEXGEN™️ Vacuum Recirculation Mill: Hockmeyer’s Answers to the Challenges of Nanoparticle Production
As a manufacturer of high-quality milling equipment, we offer the HCPN Immersion Mill as one of our answers to the challenges of nano milling. On the cutting edge of nanoparticle production, this revolutionary machine clears the path to new product development and makes the science of nanoparticle manipulation user friendly. The HCPN Immersion Mill’s unique nano milling features combine with Hockmeyer’s patented containment wall, ensuring the retention of very small media. This results in an intensely aggressive shear zone that produces very fine grinds and tight particle distributions to ensure ideal conditions for nanoparticle production and manipulation.
It offers process times up to 6x faster than conventional mills, ultrafine grinding beads below .1mm in size, and reduced operating costs thanks to a decrease in the amount of media needed. Specially designed for grinding particles into the nanoparticle range with short process times, the HCPN Immersion Mill incorporates different changes into the internal milling system while leaving the fundamental, easy-to-clean and use aspect of the immersion mill the same.
This mill is able to work so efficiently and cost-effectively thanks to the HCPN’s auxiliary chamber, which provides a secondary outer wall surrounding the internal media containment wall. During the milling process feedstock is passed out of the media field, through the media containment wall, and into the auxiliary chamber while the ultrafine media is contained within the mill. It is then pumped out of the auxiliary chamber with an external pumping mechanism that operates independently from rotation of the rotor, and back into the process vessel for continued recirculation milling. Using this technology, we are able to process with media down to .05 mm and achieve particle sizes below 50 nm in record times with maximum efficiency.
Another solution created by Hockmeyer’s innovative team is our NEXGEN™️ Vacuum Recirculation Mill, which specializes in particle size reduction with the help of a vacuum that removes excess air in the batch. Designed with portability in mind, this mill works in tight spaces, enhances efficiency, and boosts profits by reducing process times, increasing yields, and eliminating air entrapment.
While milling under vacuum, air bubbles within the agglomerates begin to expand and push apart the solids, then they separate from the solids and begin to accumulate in the mill’s upper chamber. Once enough air accumulates, it is purged intermittently by the mill, returning to the supply tank and quickly rising to the top where it is released. With the help of our NEXGEN™️ mill, you’ll achieve faster, purer particle size reduction and deagglomeration without the hassle of air bubbles in the feedstock.
Learn More About Milling Solutions From Hockmeyer Today
If you’re interested in learning more about the HCPN Immersion Mill or NEXGEN™️ Vacuum Recirculation Mill, reach out to our team to discover the difference this mill could make for your business.