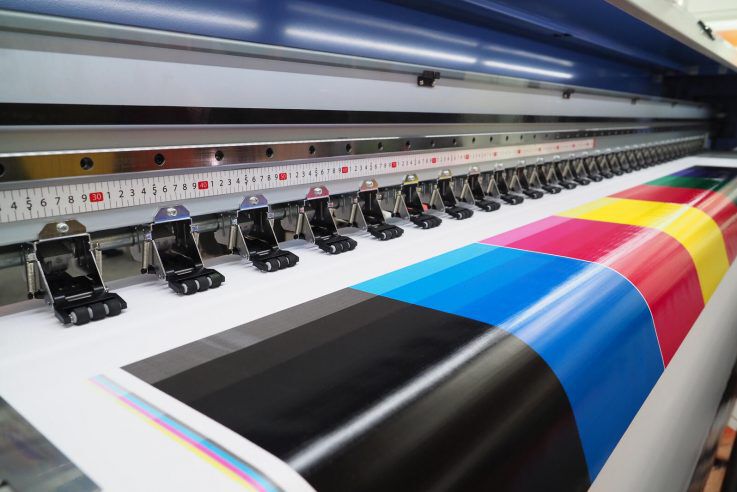
High-Quality Equipment for Ink Manufacturing
Inks play a crucial role in printing because their composition suits specific printing techniques and the surfaces they interact with, such as paper, cardboard, wood, textiles, foil, plastic, metal, and leather. The process of manufacturing printing ink is a complex and specialized one, involving the meticulous grinding of pigments to form an ink dispersion that combines resins and stabilizers to attain the desired functional attributes. By grinding the pigments to precise particle sizes, the ink can achieve the necessary color, strength, gloss, transparency, and opacity, ensuring optimal performance for various applications.
Need Help? Contact Us Today!
-
Headquarters
-
Parts & Service
Industry Benefits
Packaging Inks
Packaging inks with optimum particle distribution and enhanced stability improve color development and results in smoother ink flow during printing. The result is better print quality with sharper images, vibrant colors, and improved line definition. Additionally, this offers improved water resistance, scratch resistance, and rub resistance.
Print Media
Milling can enhance the bonding of the ink to the print media by enabling superior ink transfer, leading to sharper and more vibrant print outputs. The enhanced consistency and controlled absorbency influence ink drying time and color saturation during printing as well.
Nano Pigment Dispersions for Ink Jet
Nano pigment dispersions for inkjet printing enhance print quality and prevent inkjet printer nozzle clogging. They also maximize pigment yields and provide consistent color results.
High-Viscosity Inks
Grinding high-viscosity inks to a tight particle size distribution benefits the final product by improving the ink’s handling and application during the printing process, ensuring consistent color and a uniform appearance in the long run.
Featured Industry Solutions
-
HHL-II Dual Shaft Mixer/Disperser
Features/Options Available Sizes from laboratory units to 3500 gallons Hoist or tank mounted configuration Inverter driven motors Stainless steel or carbon steel material of construction Helical or anchor sweep low-speed…
View HHL-II Dual Shaft Mixer/Disperser
-
HHL-III Triple Shaft Mixer/Disperser
Features/Options Available Sizes from laboratory units to 3500 gallons Hoist or tank mounted configuration Inverter driven motors Stainless steel or carbon steel material of construction Helical and anchor sweep low-speed…
View HHL-III Triple Shaft Mixer/Disperser
-
NEXGEN™ Vacuum Recirculation Mill
Machine Features Flexibility for various batch volumes Hook up to any tank: portable or permanent Sanitary fittings for fast and easy cleanup High screen surface area to media ratio Greater…
View NEXGEN™ Vacuum Recirculation Mill
-
NEXGEN™ Vacuum Rotor Stator
DISPERSION TECHNOLOGY. FAST. PATENTED The process takes place in a temperature-controlled environment to preserve formulae characteristics and function. A thorough cooling system covering the chamber and return lines quickly mitigates…
View NEXGEN™ Vacuum Rotor Stator
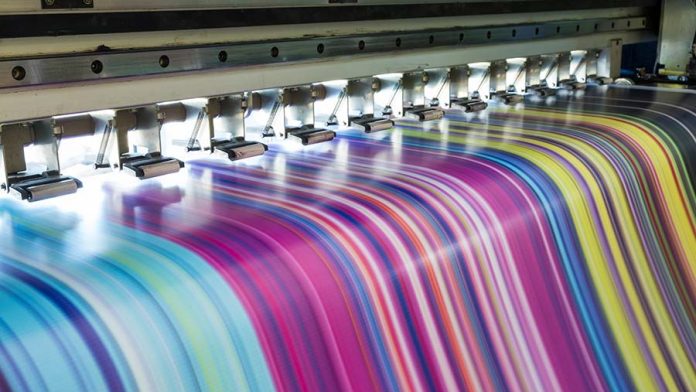
Why Choose Hockmeyer
Hockmeyer Leads the World in the Mixing, Milling, and Deagglomeration of High-Viscosity Products
Hockmeyer is an industry leader and trusted partner for businesses seeking superior solutions in milling high-viscosity products and inks, including particle size reduction, dispersion, mixing, and other process requirements. With a wide variety of industry-leading equipment and extensive experience, Hockmeyer also has a remarkable history of excellence in both customer satisfaction and innovation.
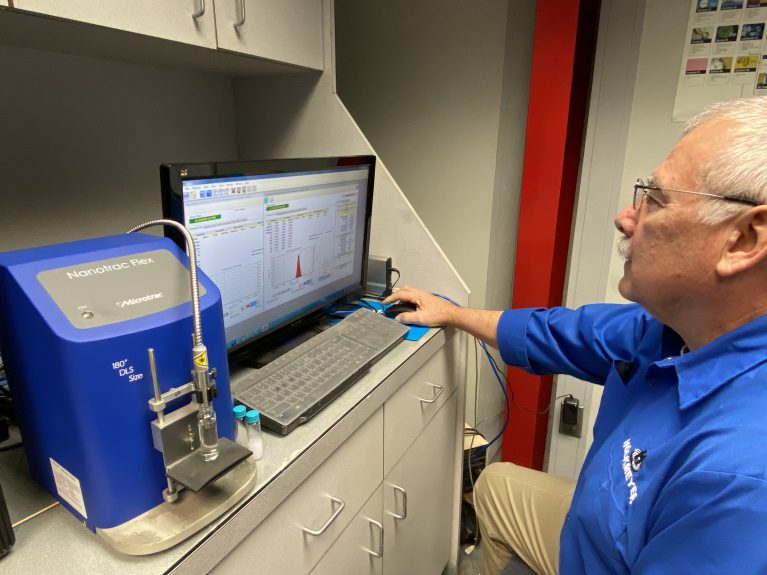
Test Your Product Free. Schedule a Test Today!
At Hockmeyer, we're committed to making your product the highest quality possible, whether you need milling, mixing, dispersion or agitation. Schedule your product to be tested in one of our demo machines and see the Hockmeyer difference for yourself.
Services
-
Field Training & Support
Hockmeyer is dedicated to providing best-in-class support to maintain the lifespan and efficiency of your Hockmeyer equipment.
-
Equipment Support Program
Learn about how Hockmeyer can provide dedicated service, maintenance, and training through our Equipment Support Program.
-
Customer Testing-Applications Lab
Don’t trust promises, trust results! Hockmeyer offers it’s Customer Service Laboratory to show you exactly how our equipment will increase your product quality and efficiency!
Printing Inks Milling Frequently Asked Questions
-
Do you provide testing for your ink manufacturing equipment?
We understand that perfecting these processes can be challenging, so we have equipped our Customer Service and Testing Facility with laboratory, pilot, and production models of our most popular equipment. Customers are encouraged to work with our team of experts and run trials to determine the optimal parameters for their product. Furthermore, we offer free initial testing!
-
How can Hockmeyer’s equipment assist in the ink manufacturing process?
The equipment used during the deagglomeration, dispersion, and milling of the pigments for printing inks makes all the difference in achieving an efficient processing method and the quality of the final product. Through innovative mixing, dispersing, and milling solutions, it is possible to make efficient, consistent, and reliable products.
-
How do you avoid foaming problems in waterborne formulas?
Avoiding foaming problems in waterborne ink formulas is crucial for improving efficiency and increasing profits. Recirculating vacuum dispersion and milling offer a solution by reducing process times, increasing yields, and eliminating air entrapment.
The NEXGEN™ equipment line addresses the issue by removing air from the product, ensuring a pure and stable dispersion without the inconvenience of air bubbles in the feedstock. The NEXGEN™ RotorStator disperses the pigment and eliminates trapped air, enabling faster and purer particle size reduction and deagglomeration. The NEXGEN™ Vacuum Recirculation Mill further reduces the pigment’s particle size, resulting in a tight size distribution, ultimately yielding a high-quality dispersion ready for letdown and final ink production.
-
How is ink made for printers?
In ink manufacturing, pigments are the most expensive component, and selecting and processing pigment is crucial for efficient production. The ink-making process involves two fundamental physical processes—wetting and deagglomeration of pigments and their uniform dispersion in the vehicle, known as dispersion. Milling is the step that reduces the particle size to a specified metric. The quality of the product and its profitability largely depend on optimizing these two processes.
-
What is used to make printing ink?
Printing ink is available in paste or liquid form and is made up of dyes or pigments derived from nitrogen-rich sources that determine the ink’s color. The ink’s base, called varnish, includes linseed oil or soybean oil, resins, solvents, and other materials and serves as a binding agent to enhance gloss and protect printed surfaces. Resins improve the ink’s binding and adhesion to printed surfaces, and additives, like lubricants, surfactants, alkali materials, and drying agents, are incorporated into the ink to modify its properties for different applications, providing rub resistance, improving printability, adjusting pH levels, and promoting faster drying.