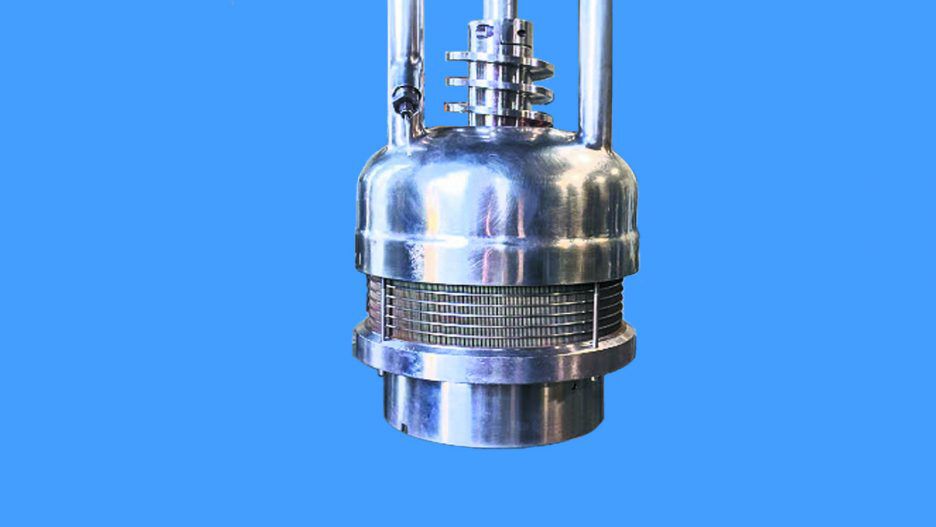
Dispersers and Immersion Mills
Immersion Milling Quick and Easy (Updated 2022)
Updated on: October 31, 2022
An Introduction to Immersion Milling
We’ve covered many other topics about immersion milling, including how milling works in a factory ecosystem, the rules of thumb for particle size reduction, and ways that recirculation vacuum mills can improve your process. However, this article covers one of our most popular topics, so we’ve decided to update it to take a closer look at the benefits of immersion mills and the differences between Hockmeyer mills and other basket mills.
Immersion Mill vs. Basket Mill: What’s the Difference?
The terms “immersion mill” and “basket mill” are often used interchangeably, but is there a difference? Actually, there isn’t. We will use these terms interchangeably for this article, but “immersion milling” is a term Hockmeyer coined when it introduced its first immersion mill. To differentiate between this Hockmeyer-specific machine and other mills, companies began calling their machines “basket mills.”
The Hockmeyer Immersion Milling Difference
Several mill companies claim their basket mills are superior and play off what they believe to be shortcomings in other mills. They contend that immersion mill technology best suits small-batch processing as well as low-viscosity and easy-to-grind products.
By contrast, our immersion mills use rapid recirculation milling technology (the same concept as in the high-energy recirculation horizontal mills) and rapidly pump the slurry through the media field many more times and more efficiently than any other mill, including horizontal or vertical mills. Remember that any external mill (horizontal or vertical) that relies upon tank-to-tank or same-tank recirculation is not a continuous process but a batch process.
The Problem With Other Basket Mills
Several basket mill manufacturers have added second and third mixing shafts to their basket design because they have low exit velocities, a byproduct of poor throughput. Without using a bottom suction device directly below the basket, the slurry bypasses the bottom of the media field (the high-energy zone). It follows the path of least resistance through the side screen.
Any product higher than a few hundred centipoises in viscosity will be motionless within a few inches of the basket, resulting in stratification during the milling process. A similar phenomenon, known as “short cycling,” occurs in horizontal mills when the slurry follows the wall of the grinding chamber to its discharge, bypassing the high-energy force of the media nearest the center shaft. This can double or sometimes triple the time required to reach product quality, resulting in a broad particle size distribution.
The Solution to Traditional Basket Mill Throughput
The solution to the problem is an upper and lower draft tube with a side and bottom screen and a suction device (lower prop) positioned within the bottom draft tube below the bottom screen. The lower draft tube propeller focuses the slurry suction exclusively from the mill’s upper level. This reduces bypass as a more significant percentage of slurry is drawn deeper into the bead field or high-energy zone before reaching the side or bottom screen discharge. The rapid uniform flow of slurry drawn down through the top and toward the mill’s bottom increases the batch throughput rate by as much as 50%.
Additionally, performance is improved when a top auger (HEC patent) is mounted within the upper draft tube above the bead field to govern the feed, especially when viscosities are above 15,000 cps.
The Hockmeyer High-Speed Disperser Immersion Mill is efficient and versatile and can operate in batch sizes from as little as 750ml to more than 5,000 liters. Its proven design can outperform horizontal, vertical, or basket-type media milling systems with tighter particle distributions in half the time. The basic machine consists of a highly polished, water-cooled, submersible rack dome with side and bottom screens and upper and lower draft tubes. A rotating hub with pegs and a removable (HEC patent) counter-peg assembly is within the basket. A top auger and bottom prop work together to enhance the dispersion flow through the bead field and out of the basket.
To accommodate different viscosity ranges, three styles of lower impellers are available to accelerate the flow through the basket (mild/moderate/aggressive). The design requires a bottom support bushing to accommodate the lower concentric propeller. The bushing is available in Rulon (a PTFE-based thermoplastic), or ceramic composition is simple, quick to replace, and inexpensive. The mill can be completely disassembled and reassembled with a new media charge within that same period when required.
The Advantage of Hockmeyer’s Immersion Mills Over Other Basket Mills
The performance difference is so significant that the immersion mill is the “Ideal Mill Design” and offers the following advantages.
- Multiuse Tanks: The machine can be designed for use in multiple tanks with various capacities, allowing flexibility in media processing and production.
- Multiple Tank Positions: 360-degree rotations allow you to position the mill and tanks in the ideal location.
- More Efficient Cleaning: Minimization of contamination, cleanup, solvent loss, and product loss, which is better for both employees and overhead costs.
- High-Quality Products: Maximize color strength, gloss, durability, and yield and create better-quality final products.
- Efficient Processing Time: The processing time is reduced by at least 70% in most trials.
- Less Material Wasted: Reduction of raw material costs by an average of 5%.
- Efficiency Increases: Highly efficient uses of small quantities of media.
- Reliable and Predictable: Consistent and predictable performance allows you to plan your production consistently.
- Various Construction Materials: Carbon steel or stainless can be used based on the application, and pegs are available in a variety of metals and ceramics.
Flexible, Smart Immersion Mill Controls
The PLC-based Auto Process II Control Center (APCII) enables the operator to run the machine on autopilot or manual control. APCII allows process temperature and grind time limits to be set on a case-by-case basis.
The automatic mode monitors batch temperature and regulates the mill to control heat. A warning horn sounds if the product temperature exceeds the operator’s lower-limit set point. The control will shut down the mill at the upper-limit set point if left unanswered. The system is designed for ease of operator interface using a simple push-button and selector switch combination. The operator can set three temperature parameters (cooling water, alarm, shutdown temperatures) and batch time.
Find the Best Immersion Million Solution for You
No matter your needs, our immersion milling solutions can help you achieve the results you’re looking for. If you’re interested in learning more, we’re ready to help and look forward to hearing from you. Click here to contact us today, or learn more about our product testing lab.