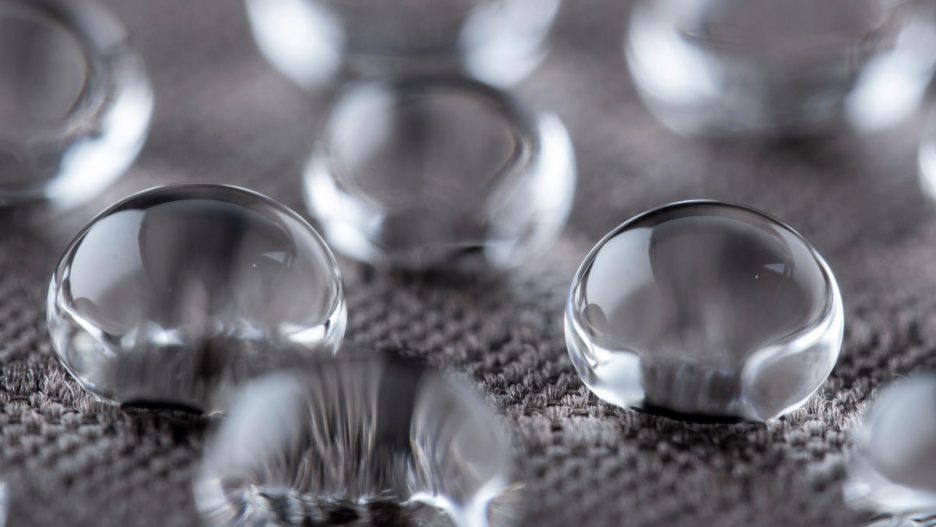
Industry News
Advancements in Milling Technology: What’s New in the Industry?
The manufacturing world has advanced to such an extent that it is virtually unrecognizable from what it was when Hockmeyer Equipment Corporation began almost a century ago. With each technological leap forward, new tools and systems become available to improve processes, efficiency, cost-effectiveness, and the quality of the resulting products.
In today’s blog, we will examine some of the latest advancements in milling technology and their impact on various parts of the manufacturing space.
Nanotechnology
Nanotechnology—anything pertaining to particles measuring less than 100 nanometers—has revolutionized numerous industries in astonishing ways, and its impact on milling technology is profound.
The ability to manipulate materials at the nanoscale has led to several significant advancements; in particular:
Antimicrobial Paints and Coatings
Nanoparticles can be engineered to have antimicrobial properties, making them ideal for use in paints and coatings. These nano-enhanced products are particularly crucial in environments where hygiene is paramount, such as hospitals and food processing plants.
Advancements in mixing technology ensure that these nanoparticles are evenly distributed, enhancing the coatings’ overall safety and effectiveness.
Increased Bioavailability of Oral Drugs
In the pharmaceutical industry, nanotechnology has enabled the creation of medicines with increased bioavailability—that is, a greater fraction of the administered dose reaches the systemic circulation in the body. By reducing particle size to the nanoscale, drugs can be absorbed more efficiently by the body.
Advanced milling equipment is crucial for achieving the precise particle size and distribution necessary for these high-performance medications.
Enhanced Effectiveness and Minimized Environmental Impact of Agrochemicals
Nanotechnology also offers significant benefits in agriculture. In particular, it can enhance the effectiveness of agrochemicals, ensuring that active ingredients are delivered more efficiently to plants. This targeted delivery reduces the chemicals needed, minimizing harmful environmental impacts.
Advanced milling technologies are essential for producing these nano-enhanced agrochemicals with consistent quality, playing a direct role in the supply chain of the crops we all rely on.
Automated Process Control and In-Line Particle Characterization
Two of the most groundbreaking advancements in milling technology are automated programmable controls and in-line particle characterization. Programmable controls create a connected manufacturing ecosystem for predictable and consistent production with integrated recipes, operator work instructions, and multiple data-gathering points for live reporting. Sensors for temperature, elapsed time, flow, vacuum, pump pressure, speed, kW draw, and maintenance alerts are preset to slow, speed up, or stop the machine based on product-specific parameters.
New technology also enables real-time monitoring of particle size, shape, and distribution during the milling process. Instead of relying on periodic sampling and offline analysis, in-line characterization provides continuous data, allowing for immediate adjustments and optimization.
This real-time feedback loop not only improves product quality but also increases efficiency by reducing downtime and minimizing waste.
Integrating sensors and real-time analysis tools means that the milling process can be automatically adjusted based on the particle characteristics. Once the desired particle size and distribution have been achieved, the system can stop the process autonomously.
This not only ensures a consistent product quality but also optimizes resource use, lowering energy consumption and operational costs by reducing the amount of manual operator input required.
A Focus on Sustainability
As in so many industries, sustainability and increased environmental awareness are major driving forces behind recent advancements in mixing technology. Manufacturing companies are increasingly seeking ways to reduce their environmental footprint while maintaining high productivity.
The three core pillars of sustainability in milling and mixing are lowering energy usage, reducing waste, and improving safety protocols. Innovations such as energy-efficient motors, optimized mixing protocols, and eco-friendly materials are becoming standard across the industry.
Hockmeyer is committed to sustainability, continuously developing technologies that not only meet but also exceed environmental standards. Our NEXGEN™ immersion mill represents the best in environmentally conscious particle reduction technology, often lowering milling time by up to 80% versus traditional milling methods and reducing waste.
Precision Temperature Control
Temperature control is critical in many mixing and milling processes and affects the quality of the final product.
Many materials commonly used in manufacturing, from pigments to polymers and even certain metals, exhibit temperature-dependent characteristics. Precise temperature control ensures that materials are processed within their ideal temperature range, improving product quality and extending the lifespan of the mixing equipment.
Recent technological advancements have led to more precise temperature-control mechanisms. These innovations include advanced cooling and heating systems that maintain optimal temperatures throughout the process, even in high-shear or high-energy environments.
Hockmeyer: The Best in Advanced Milling Technology
Here at Hockmeyer, we consistently strive to grow, develop, and innovate, improving the technologies that have made us the go-to name in milling and mixing solutions for decades. Our machines represent the cutting edge of these technologies, providing efficient, cost-effective, and eco-friendly solutions for companies across numerous industries.
If you would like to learn more about any of our machines and how they can help you improve your processes and meet your business goals, please contact us to schedule a lab trial. Our goal is to improve your processes and increase your profits.