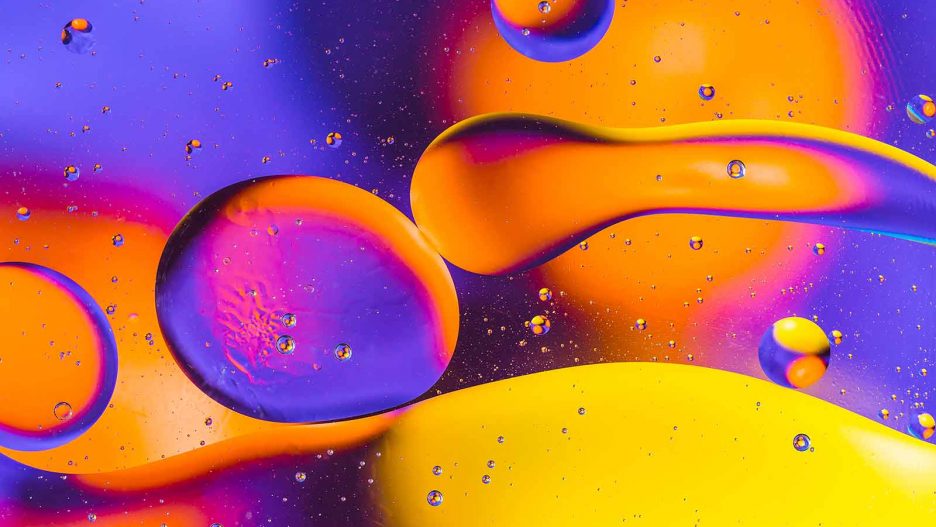
Industry Information
Key Points to Know When Mixing and Dispersing High- and Low-Viscosity Fluids
When you’re blending liquids of both high and low viscosities, your desired end result is usually a uniform, well-blended mixture. This goal is typically easily achieved in low-viscosity materials, but when combining these substances with highly viscous materials or mixing high-viscosity fluids on their own, it can be a challenge to reach your desired level of uniformity. The good news? Hockmeyer’s line of mixing and dispersing equipment has a well-deserved reputation for excellent performance and reliability thanks to our decades of experience in the industry, and our machines will help you to get the job done. However, before you get started, here are a few key points to keep in mind.
Start with the basics: high-viscosity liquids vs. low-viscosity liquids
How can we tell the difference between high-viscosity and low-viscosity liquids? A material’s viscosity is a measure of its resistance to flow. A liquid with a high internal resistance to flow (like honey) has a high viscosity, while a liquid with a low internal resistance to flow (like room-temperature water) is classified as a low-viscosity fluid. Whether you’re mixing high-viscosity substances, low-viscosity liquids, or a combination of the two, mixing involves the systematic creation of a single material by intermingling two or more different individual ingredients or particles. These ingredients are usually fed into a rotating impeller through its trailing edge.
Mixing is very similar to dispersion since they both involve blending materials together. However, mixing employs a “flow-driven” process through which two or more liquids are combined, and an additional soluble solid can be dissolved. a method to cause separate ingredients otherwise independent from one another to interface as a result of an external force. While mixing is flow-driven, dispersion is a shear-driven process. During the dispersion process, a machine breaks down particles (deagglomeration), to create a uniform mixture in a process called “wetting.” If these particles stayed grouped together, their total surface area wouldn’t be able to combine with a liquid solution.
Understanding the “flow” of your materials and the mixing and dispersing processes
Understanding the flow of the different liquids you’re working with is essential to successful mixing and dispersion, and there are three types of flow that can be achieved: laminar flow, transitional flow, and turbulent flow. Low-viscosity mixes have higher turbulence and extended flow. So, the higher the viscosity, the less turbulent the flow.
An additional factor that’s important to consider when beginning the mixing or dispersing process is a substance’s Reynolds number. This number is used to measure turbulence, helps to predict how a liquid will flow, and takes into account the substance’s viscosity, flow velocity, and density. This number is important to note, because as a substance’s Reynolds number increases and materials transition from laminar to turbulent flow, mixing intensifies. By contrast, when a substance’s Reynolds number decreases mixing becomes less intense and more streamlined.
How can you decide which mixer or disperser is right for you?
Now that we’ve reviewed the basics, there are a few additional factors to consider before deciding which mixing or dispersing equipment is right for you. It’s essential to consider all of the elements that have the power to impact the mixing or dispersing process, including:
- Shear: this phenomenon usually occurs at low Reynolds numbers and occurs because of the differing velocities of various streamlines. As a result of the stress created between particles as a result of shear, additional heat is generated, and particles tend to be torn apart. Shear is helpful in deagglomeration, but it can be detrimental when attempting to sustain particle size during mixing.
- Temperature boundaries: when the temperature must be maintained within a certain range for your mixing project, additional equipment can be required to heat or cool the system. In challenging cases, this may include computer-controlled devices that act on command to control heat exchange. Each of these devices come with extra costs for installation, operating, and maintenance.
- Economic considerations: from time to time, the “dream” mixing or dispersing system you may want for your project doesn’t make the most economic sense. A system’s projected profitability and length of time the product may be in demand should be equal to not only the costs of the system, but also the anticipated start-up time required.
Ready to get started?
Whatever your needs, our mixers and dispersers are designed by an experienced engineering staff incorporating information from customers, our own R&D Laboratory, and years of data from Hockmeyer multi-shaft mixers. We’ve highlighted a few of our most popular mixers below to give a sense of the basic features that each brings to the table.
For combining products with low to medium viscosities, we’d recommend our HVI Hoist Mounted Dispersers, or our HVIE Hoist Mounted (Economy) Dispersers. With a robust, durable design and construction, Hockmeyer’s line of HVI dispersers allow for variable speed, single shaft mixing to disperse, dissolve, deagglomerate and emulsify solid particles in a liquid. The HVIE line offers similar features, along with all of the quality and durability that Hockmeyer is known for, at a lower price point.
Both of these lines of machines use an “F” blade meant for lower fluid viscosities, which creates a vortex that allows for proper dispersion of particles throughout your product mixture. This style of blade is a popular all-around tool for all high-speed dispersers, and our “F” blade is made of heavy gauge 304 stainless steel to ensure a longer life and better dispersion.
When working with high-viscosity products, Hockmeyer’s multi-shaft mixers like the HHL-III or HHL-II Triple Shaft Mixer/Dispersers can tackle even the most challenging high-viscosity mixing jobs. These multi-shaft mixers have a center-mounted low-speed helical or anchor blades which sweep the mixing vessel wall and one or more high-speed dispersion shafts, which provide shear to disperse or dissolve ingredients. By using these blades, our HHL-III and HHL-II lines generate a uniform mix by moving product away from the tank walls and efficiently folding thicker materials into your mixture.
Ultimately, the truth is that there is no one mixer that can satisfy all mixing and dispersing needs. From batch mixers and laboratory mixers to high viscosity mixers, single shaft mixers and dispersers, each machine can help you to achieve your desired level of uniformity, depending on the materials you’re blending together. While viscous mixing and dispersing isn’t a simple task, it can be made easier by understanding the basics of mixing, pinpointing your particular needs, and asking the right questions.