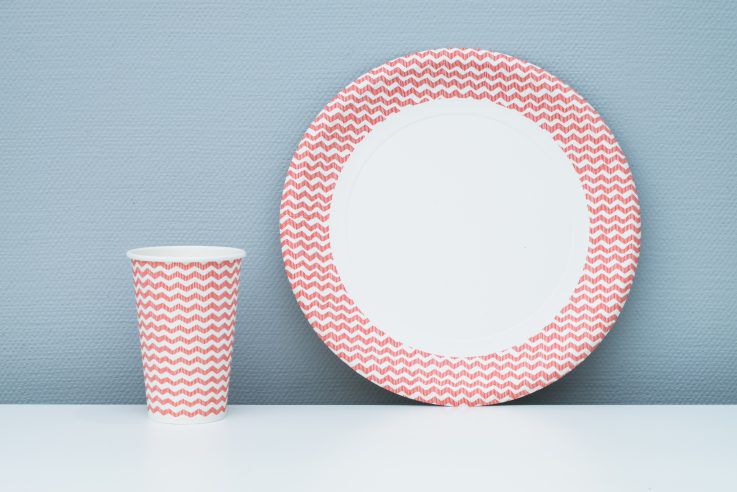
Enhance Your Paper Coating Processing Through Industry-Leading Milling, Mixing, and Dispersion Equipment
Paper coatings, which are composed of pigments, binders, additives, and solvents, are a key component of many paper products and enhance properties such as smoothness, gloss, and printability. The particle size distribution of paper coatings significantly influences your paper’s quality and performance. A controlled particle size distribution creates a uniform coating, improving printability and appearance and impacting rheological behavior, while a wider range can cause unwanted viscosity variations and frustrating challenges in maintaining consistent coating thickness.
Closely managing particle size ensures that your desired viscosity and rheology are achieved for optimal application. A narrow distribution guarantees even particle distribution, providing an appealing paper surface for the finished product. Binders controlling particle size encase pigments, boosting the coating’s integrity, adhesion, and durability. Smaller particles enhance light scattering for opacity and brightness, aiding optical properties, and optimized distribution allows proper ink penetration, refining color reproduction and print quality. Finally, smaller particles can prevent the defects and weak paper bonding that can result from uneven drying due to varied particle sizes. The greater consistency of smaller particles ensures more reliable outcomes.
Need Help? Contact Us Today!
-
Headquarters
-
Parts & Service
Industry Benefits
Paper Coatings
Paper coatings enhance paper products’ properties with pigments, binders, and additives. Particle size distribution affects quality, influencing smoothness, gloss, print, and ink adhesion within these coatings. Better particle control ensures uniformity, optimal application, and improved print quality.
Adhesive Resins
High-quality adhesive resins keep paper coatings in place. Ensuring smaller particles means they disperse uniformly, enhancing adhesive resin distribution for more consistent coatings. Improved resin adhesion bolsters your coating’s integrity, even under deformation, and the increased surface area from finer particles fosters flexibility and clarity.
Temperature Sensitive
Thermal responsiveness is important to the paper coating process, especially in thermal printing and thermochromic labels. Particle size affects thermal responsiveness because finer particles provide an increased surface area, enabling quicker and more sensitive temperature responses. Smoother coatings can make a big difference with temperature-sensitive materials and yield more crisply printed images.
Featured Industry Solutions
-
HCP Drum Mill
Machine Features 20 Hp 115″ Overall Height, 36″ Stroke, 22″ Width Water-cooled dome for temperature control Upper auger to consistently feed material into the mill chamber Variable Frequency Inverter A…
View HCP Drum Mill
-
HCP Immersion Mill
Machine Features Multiple tank positions with 360º rotation available Minimal cross-contamination, easy clean-up, and low solvent loss Maximizes color development, strength, gloss, durability, and yield Reduction of process time versus…
View HCP Immersion Mill
-
HHL-II Dual Shaft Mixer/Disperser
Features/Options Available Sizes from laboratory units to 3500 gallons Hoist or tank mounted configuration Inverter driven motors Stainless steel or carbon steel material of construction Helical or anchor sweep low-speed…
View HHL-II Dual Shaft Mixer/Disperser
-
HHL-III Triple Shaft Mixer/Disperser
Features/Options Available Sizes from laboratory units to 3500 gallons Hoist or tank mounted configuration Inverter driven motors Stainless steel or carbon steel material of construction Helical and anchor sweep low-speed…
View HHL-III Triple Shaft Mixer/Disperser
-
HVI Hoist Mounted Disperser
Variable speed, single-shaft mixer to disperser, dissolve, deagglomerate & emulsify solid particles in a liquid.
View HVI Hoist Mounted Disperser
-
HVIE Hoist Mounted Disperser Air/Oil Lift
Machine Features Available in explosion-proof (XP) and non-explosion-proof (TEFC) packages Standard controls Air-over-oil lift Standard post mixer What is a Disperser? A Disperser is a single-shaft mixer used to break…
View HVIE Hoist Mounted Disperser Air/Oil Lift
-
NEXGEN™ MICRO MILL
Machine Features Mill and deaerate at once Greatest throughput of all media mills on the market Nano-particle size capability Media size as small as .03mm Sanitary fittings for fast and…
View NEXGEN™ MICRO MILL
-
NEXGEN™ Vacuum Recirculation Mill
Machine Features Flexibility for various batch volumes Hook up to any tank: portable or permanent Sanitary fittings for fast and easy cleanup High screen surface area to media ratio Greater…
View NEXGEN™ Vacuum Recirculation Mill
-
NEXGEN™ Vacuum Rotor Stator
DISPERSION TECHNOLOGY. FAST. PATENTED The process takes place in a temperature-controlled environment to preserve formulae characteristics and function. A thorough cooling system covering the chamber and return lines quickly mitigates…
View NEXGEN™ Vacuum Rotor Stator
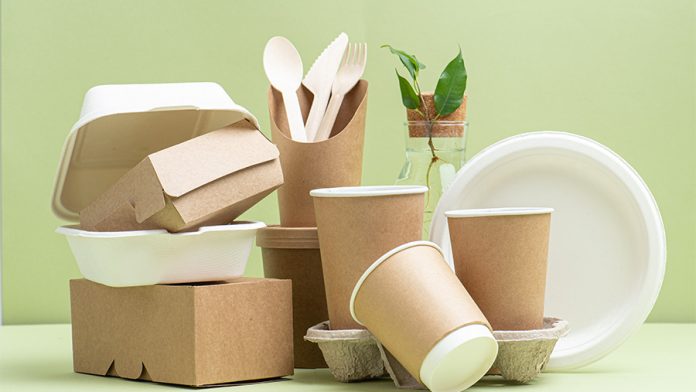
Why Choose Hockmeyer
Milling, Mixing, and Dispersion Equipment for Paper Coating Manufacturers
Hockmeyer is a trusted partner for businesses seeking high-quality solutions in particle size reduction, dispersion, mixing and milling, and other process requirements. With its range of industry-leading equipment and wealth of experience, the company has a rich history of excellence and has solidified its place at the forefront of the paper coatings industry by prioritizing customer satisfaction and innovation.
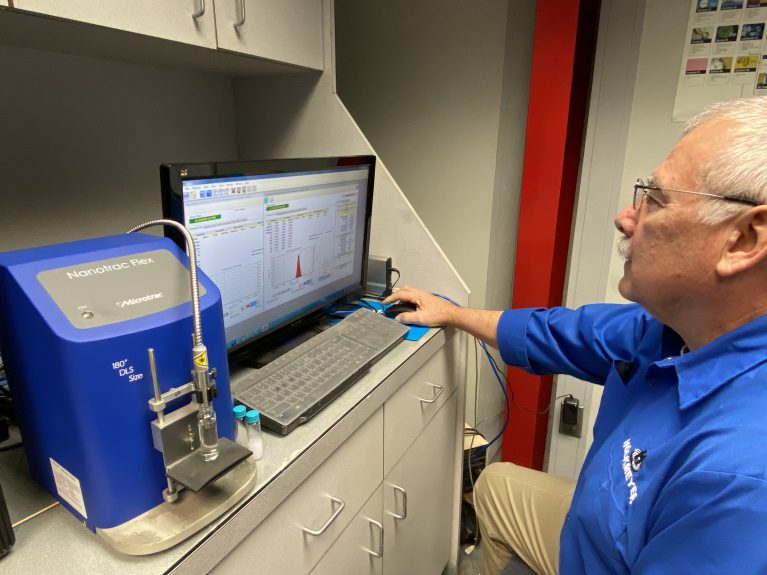
Test Your Product Free. Schedule a Test Today!
At Hockmeyer, we're committed to making your product the highest quality possible, whether you need milling, mixing, dispersion or agitation. Schedule your product to be tested in one of our demo machines and see the Hockmeyer difference for yourself.
Services
-
Field Training & Support
Hockmeyer is dedicated to providing best-in-class support to maintain the lifespan and efficiency of your Hockmeyer equipment.
-
Equipment Support Program
Learn about how Hockmeyer can provide dedicated service, maintenance, and training through our Equipment Support Program.
-
Customer Testing-Applications Lab
Don’t trust promises, trust results! Hockmeyer offers it’s Customer Service Laboratory to show you exactly how our equipment will increase your product quality and efficiency!
Paper Coating Processing Frequently Asked Questions
-
How can Hockmeyer’s equipment assist in the paper coating manufacturing process?
Hockmeyer’s rapid flow and recirculation technologies play a crucial role in the dispersion process, ensuring the consistent and tight particle size distributions that are vital for maintaining high product quality in paper coatings. Machines like the HCP Immersion Mill, the HHL line of dispersers/mixers, the HCP Immersion Mill, and the HVI Hoist Mounted Disperser are all great options for manufacturing paper coatings. Furthermore, Hockmeyer’s innovative equipment improves efficiency, overall operational effectiveness, and productivity by drastically reducing process times.
-
Do you provide testing for your paper coating processing equipment?
Yes! We understand that the process of finding the right equipment can be challenging, so we have equipped our testing facility with laboratory and scalable pilot models of our most popular offerings. We also offer free initial testing to help you evaluate the performance of the equipment and find the paper coatings solution that best fits your needs.
-
Why is the paper coating process important?
Coatings are applied in layers of different substances to improve qualities like printability, smoothness, gloss, and durability, and the paper coating process is vital for enhancing the finished product’s properties and performance for specific uses. The process involves several steps, including coating formulation preparation (mixing pigments, binders, additives, and solvents to create a coating mixture), mixing and dispersion to ensure a uniform mixture to prevent clumping or settling, and applying the coating using methods like roll coating, blade coating, air knife coating, or size press coating based on thickness, paper type, and formulation. The process is completed through drying or curing, which removes solvents and enhances binder adhesion and durability through drying or chemical reactions.
-
What are the particle coating methods in the paper coating manufacturing process?
Particle coating methods are vital in paper coating manufacturing, providing various techniques for enhancing paper properties and achieving specific effects on the paper’s surface. Air knife coating uses controlled air to deposit particle-laden fluid uniformly onto the paper. This method ensures even coatings with controlled thickness. In press coating, the paper passes through a particle-laden liquid bath that enhances properties like smoothness and printability. Spray coating involves dispersing particles in liquid and applying the mixture with precision. This method is versatile, allowing for textured surfaces and visual effects. Gravure coating employs engraved rollers to transfer the coating, providing high-quality, consistent fine coatings.
Other methods include offset printing with dry powder, which modifies offset presses to apply powders, adding specific visual effects to printed materials. Electrostatic coating charges particles and applies them using an electric field, a process that is useful for toner-based printing and textures. Finally, hot melt coating melts solid coatings, applying them as a fluid that solidifies upon cooling, serving various applications.